Polymrization method of preparing polyphonyl ether/phenylethylene kind polymer alloy in reactor
A technology of styrene and polyphenylene ether, which is applied in the field of preparing polyphenylene ether/styrene polymer alloys, can solve the problems of polymer degradation and discoloration, and achieve the effect of preventing melt degradation and reducing the process of melt blending
- Summary
- Abstract
- Description
- Claims
- Application Information
AI Technical Summary
Problems solved by technology
Method used
Image
Examples
Embodiment 1
[0029] Using a 500mL reactor with gas inlet and outlet, stirring paddle, thermometer and constant temperature jacket, the preparation of polyphenylene ether / polystyrene alloy was carried out as follows.
[0030] Add 250 mL of distilled water containing 10 grams of sodium hydroxide into the reaction kettle, control the temperature of the reaction kettle at 40° C., and stir to completely dissolve the sodium hydroxide. Then, 2.44 g of 2,6-dimethylphenol was added to the aqueous solution and stirred until completely dissolved, while air was blown in. Separately prepare a mixed solution containing 0.50 g of cuprous chloride, 1.2 g of ethylenediamine, and 10 mL of water. The mixed solution was added to the reaction kettle, and 145 mg of sodium lauryl sulfate was added. After stirring and reacting for 1 hour, add 2.44g styrene, increase the stirring rate to 1500rpm, after reacting for 18 hours, add 0.00244g dibenzoyl peroxide, remove the air in the above-mentioned reaction kettle wi...
Embodiment 2~7
[0032] Basically repeat the procedure described in Example 1, the difference is the copper compound and the amine compound, see Table 1.
[0033]
Embodiment 8
[0035] Using a 500mL reactor with gas inlet and outlet, stirring paddle, thermometer and constant temperature jacket, the preparation of polyphenylene ether / polystyrene alloy was carried out as follows.
[0036] Add 250 mL of distilled water containing 10 grams of potassium hydroxide into the reaction kettle, control the temperature of the reaction kettle at 50° C., and stir to completely dissolve the potassium hydroxide. Then, 21.2 g of 2-methyl-6-phenylphenol was added into the aqueous solution and stirred until completely dissolved, while oxygen was introduced to keep the oxygen pressure in the reactor at 1 atm. 1.316 g of potassium ferricyanate and 1.45 g of sodium lauryl sulfate were then added. After stirring and reacting for 1 hour, 10.6 g of styrene and 0.6 g of α-methylstyrene were added, and the stirring rate was increased to 1000 rpm. After reacting for 18 hours, add 0.053 g of azobisisobutyronitrile, use nitrogen to remove the air in the reaction kettle, seal it, ...
PUM
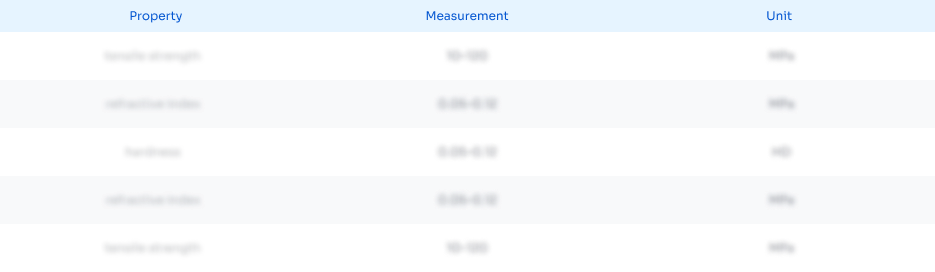
Abstract
Description
Claims
Application Information

- R&D
- Intellectual Property
- Life Sciences
- Materials
- Tech Scout
- Unparalleled Data Quality
- Higher Quality Content
- 60% Fewer Hallucinations
Browse by: Latest US Patents, China's latest patents, Technical Efficacy Thesaurus, Application Domain, Technology Topic, Popular Technical Reports.
© 2025 PatSnap. All rights reserved.Legal|Privacy policy|Modern Slavery Act Transparency Statement|Sitemap|About US| Contact US: help@patsnap.com