High strength ultrafine fiber simulation composite lether and its manufacturing method
A technology of ultra-fine fibers and manufacturing methods, applied in the direction of textiles and papermaking, etc., can solve the problems of large differences in tensile strength and insufficient high resilience, and achieve the effects of small deformation, good elasticity, and reliable manufacturing methods
- Summary
- Abstract
- Description
- Claims
- Application Information
AI Technical Summary
Problems solved by technology
Method used
Image
Examples
Embodiment 1
[0034] Nylon-6 and polyethylene are mixed and melted in 70:30 parts by weight, and drawn by a spinning machine to make (3-7)D×(30-65)mm sea-island composite fibers; using textile technology, the The above-mentioned island-in-the-sea composite fiber is made into a woven fabric with a thickness of 0.3mm; the above-mentioned island-in-the-sea composite staple fiber is made into an average grammage of 160g / m by non-woven fabric weaving technology 2 , a non-woven fabric with a thickness of 0.5mm; figure 1 Superimposed in the same way, at a needle punching density of 1200 needles / cm 2 Needle-punched under the same conditions to make the base fabric. Vacuum impregnation treatment with 18% polyurethane impregnation solution, passing the impregnation solution at a uniform speed, so that polyurethane is impregnated in the fiber gap, the impregnation amount of polyurethane is 25% of the weight of the base cloth, and then the concentration is 40%, the temperature is 50 The DMF aqueous s...
Embodiment 2
[0037] Nylon-6 and polyethylene are mixed and melted in 65:35 parts by weight, and drawn by a spinning machine to make (3-7)D×(30-65)mm sea-island composite fibers; using weaving technology, the The above-mentioned island-in-the-sea composite fiber is made into a woven fabric with a thickness of 0.5 mm; the above-mentioned island-in-the-sea composite short fiber is made into an average grammage of 300 g / m by using non-woven fabric manufacturing technology 2 , a non-woven fabric with a thickness of 1.0mm; the above-mentioned two-layer non-woven fabric and one-layer woven fabric image 3 Superimposed in the same way, at a needle density of 1500 needles / cm 2 Acupuncture compound under the conditions to make the base fabric; use 20% polyurethane impregnating liquid for vacuum impregnation treatment, pass the impregnating liquid at a uniform speed, so that the polyurethane is impregnated in the fiber gap, and the impregnation amount of polyurethane is 35% of the weight of the base ...
Embodiment 3
[0040] Polyester and polyvinyl alcohol are mixed and melted in 80:20 parts by weight, and drawn by a spinning machine to make (3-7) D × (30-65) mm sea-island composite fibers; using weaving technology, the The above-mentioned island-in-the-sea composite fiber is made into a woven fabric with a thickness of 0.5 mm; the above-mentioned island-in-the-sea composite short fiber is made into an average grammage of 300 g / m by non-woven fabric weaving technology 2 , a non-woven fabric with a thickness of 1.0mm; figure 2 Laminated in the same way and bonded with porous polyurethane to make a composite base cloth; use 25% polyurethane impregnation solution for vacuum impregnation treatment, pass the impregnation solution at a uniform speed, so that polyurethane is impregnated in the fiber gap, and the impregnation amount of polyurethane is the weight of the base fabric 20% of 20%, and then use a concentration of 60% and a DMF aqueous solution at a temperature of 50°C to solidify the po...
PUM
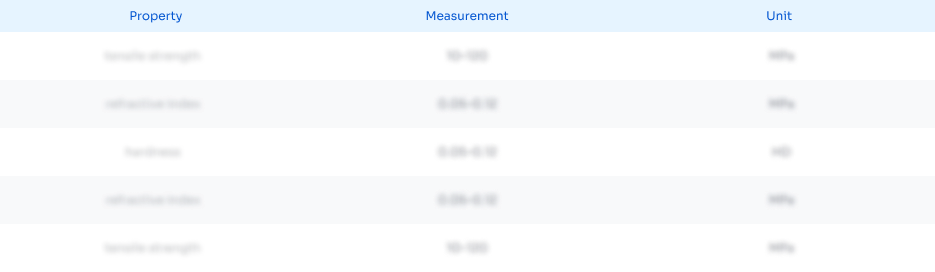
Abstract
Description
Claims
Application Information

- R&D
- Intellectual Property
- Life Sciences
- Materials
- Tech Scout
- Unparalleled Data Quality
- Higher Quality Content
- 60% Fewer Hallucinations
Browse by: Latest US Patents, China's latest patents, Technical Efficacy Thesaurus, Application Domain, Technology Topic, Popular Technical Reports.
© 2025 PatSnap. All rights reserved.Legal|Privacy policy|Modern Slavery Act Transparency Statement|Sitemap|About US| Contact US: help@patsnap.com