Electric power steering system and method having abnormality compensation function
An electric steering system and abnormal technology, applied in electric steering mechanism, power steering mechanism, automatic steering control components, etc., can solve problems such as lack of power assistance and increased steering force
- Summary
- Abstract
- Description
- Claims
- Application Information
AI Technical Summary
Problems solved by technology
Method used
Image
Examples
Embodiment Construction
[0017] Such as figure 1 As shown, in the electric power steering system 1, the steered wheels 10 are connected to the steered shaft 12a. The lower end of the steering shaft 12a is connected to a torque sensor 40 . The upper end of the pinion shaft 12 b is connected to a torque sensor 40 . At the lower end of the pinion shaft 12b, a pinion not shown in the figure is provided. In the steering gearbox 16 the pinion meshes with a rack 18 . One end of the tie rod 20 is connected to one end of the rack gear 18 . The other end of the tie rod 20 is connected to the front wheel 24 through the steering arm 22 . Similarly, one end of another tie rod 20 is connected to the other end of the rack 18 . The other end of the other tie rod 20 is connected with the other front wheel 24 through the steering arm 22 . Furthermore, on the pinion shaft 12b, the assist motor 15 communicates with the reduction gear 17 .
[0018] A speed reduction device 17 composed of gears or the like transmits...
PUM
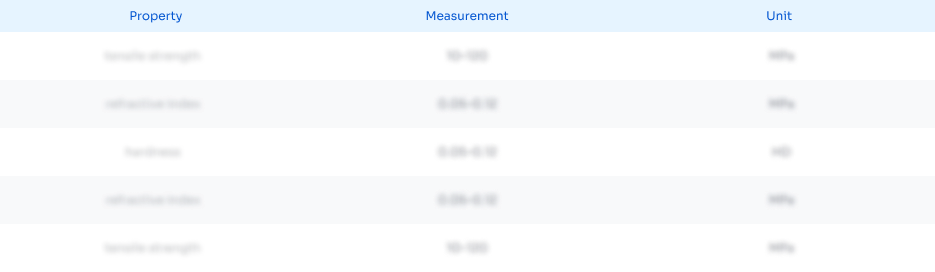
Abstract
Description
Claims
Application Information

- R&D
- Intellectual Property
- Life Sciences
- Materials
- Tech Scout
- Unparalleled Data Quality
- Higher Quality Content
- 60% Fewer Hallucinations
Browse by: Latest US Patents, China's latest patents, Technical Efficacy Thesaurus, Application Domain, Technology Topic, Popular Technical Reports.
© 2025 PatSnap. All rights reserved.Legal|Privacy policy|Modern Slavery Act Transparency Statement|Sitemap|About US| Contact US: help@patsnap.com