Method for producing ball mill burnisher
A production method and ball mill technology, which are applied to casting molding equipment, casting molds, cores, etc., can solve the problems of complex production process and high production cost, and achieve the effects of simple operation, low production cost, and improved wear resistance.
- Summary
- Abstract
- Description
- Claims
- Application Information
AI Technical Summary
Problems solved by technology
Method used
Image
Examples
Embodiment 1
[0021] A method for producing ball mill grinding rods with a size of φ30mm×50mm is that the chemical composition of the grinding rods is selected as (wt, %): 1.8C, 0.9Si, 0.8Mn, 0.2V, 0.09Ti, 2.5Cr, 0.4Cu, 0.15 Ni, P, Sfigure 1 ). The molten steel is smelted in an intermediate frequency induction furnace. The tapping temperature is 1450~1500℃, the pouring temperature is 1400~1450℃, and the box is boxed 10-15 minutes after pouring. The air quenching temperature is 800~900℃. After cooling, it is polished and cleaned. Library.
Embodiment 2
[0023] A method for producing ball mill grinding rods with a size of φ30mm×50mm is that the chemical composition of the grinding rods is selected as (wt, %): 2.0C, 1.3Si, 1.0Mn, 0.2V, 0.09Ti, 2.7Cr, 0.3Cu, 0.10 Ni, P, Sfigure 1 ). The chemical composition of the grinding rod is (wt,%): the molten steel is smelted in an intermediate frequency induction furnace, the tapping temperature is 1450~1500℃, the pouring temperature is 1400~1450℃, the boxing is 10-15 minutes after pouring, and the air quenching temperature is 800~900℃, after cooling, it will be polished and cleaned before storage.
PUM
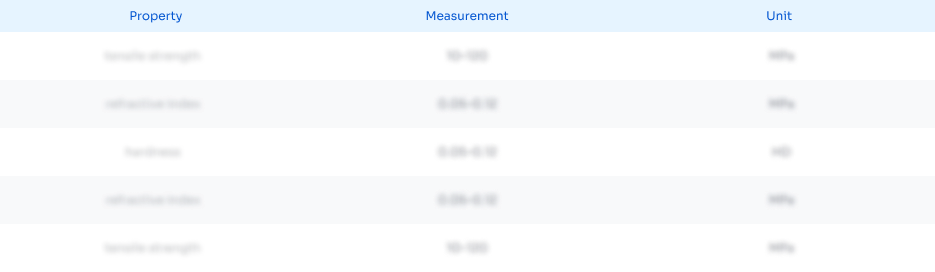
Abstract
Description
Claims
Application Information

- Generate Ideas
- Intellectual Property
- Life Sciences
- Materials
- Tech Scout
- Unparalleled Data Quality
- Higher Quality Content
- 60% Fewer Hallucinations
Browse by: Latest US Patents, China's latest patents, Technical Efficacy Thesaurus, Application Domain, Technology Topic, Popular Technical Reports.
© 2025 PatSnap. All rights reserved.Legal|Privacy policy|Modern Slavery Act Transparency Statement|Sitemap|About US| Contact US: help@patsnap.com