Controller for synchromotor, electric equipment and module
A technology of synchronous motor and control device, applied in the direction of motor control, motor generator control, AC motor control, etc., can solve the problems of vibration and noise, difficulty of synchronous motor, etc., and achieve the effect of suppressing vibration and noise
- Summary
- Abstract
- Description
- Claims
- Application Information
AI Technical Summary
Problems solved by technology
Method used
Image
Examples
Embodiment 1
[0032] figure 1 It is a block diagram illustrating the system configuration of Embodiment 1 of the AC motor control device of the present invention. The control device of this embodiment 1 is composed of the following parts: the instruction 100 of the host control device gives the motor a speed command ω r * The speed command generator 1; the controller 2 that calculates the AC applied voltage of the motor and converts it into a pulse width modulation signal (PWM signal) output; the converter (inverter) 3 driven by the PWM signal; the converter 3 that provides power A converter (converter) 4; a PM motor 5 as a control object; a compressor 6 as a load of the PM motor; and a current detector 7 for detecting a current I0 supplied from the converter 4 to the inverter 3 .
[0033] The controller 2 is composed of the following parts: According to the current I0 detected by the current detector 7, the three-phase AC current I flowing on the PM motor 5 is reproduced by calculation i...
Embodiment 2
[0068] Below, use Figure 9 Example 2 of the present invention will be described.
[0069] In Example 1, for the torque ripple vibration frequency ω d , importing a sine wave transfer function with infinite gain. As a result, ω contained in the torque ripple d The components are removed, and the distortion of the driving current of the PM motor increases instead. Since it follows the load torque variation instantaneously, it is unavoidable that the instantaneous current fluctuates greatly. For this reason, the efficiency of the PM motor deteriorates, and abnormalities such as overcurrent trips due to peak currents occur. Therefore, it can be said that the reduction effect of vibration and noise is alleviated as a whole, and on the contrary, it is practical to adjust a compromise point for preventing current distortion.
[0070] Embodiment 2 is to add the function of adjusting the suppression ability to the suppression effect of the periodic disturbance.
[0071] Figure ...
Embodiment 3
[0075] In Embodiments 1 and 2, as a torque controller, the vibration frequency ω of torque ripple d A transfer function with the maximum gain (infinity in Embodiment 1) is introduced. In these controllers, the convergence response of the ripple component is determined by the magnitude of the control gain (control gain 222, or control gain 222B) of the output stage at the final terminal.
[0076] However, the relationship between the set value of these control gains and the actual response time is complicated, and they are studied by making a board diagram, or obtained by simulation tests or actual measurements. Therefore, a lot of effort is required in the adjustment work.
[0077] In Embodiment 3, a torque control device for simplifying adjustment work is provided.
[0078] Figure 10 A configuration example of the torque controller 22C in the third embodiment is shown. by replacing figure 1 Embodiment 3 can be realized by using this torque controller 22C.
[0079] exis...
PUM
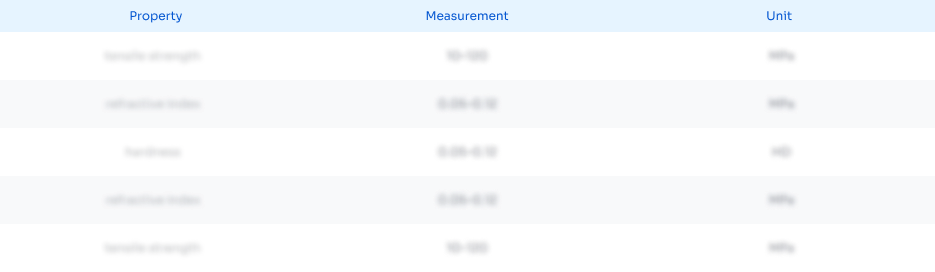
Abstract
Description
Claims
Application Information

- Generate Ideas
- Intellectual Property
- Life Sciences
- Materials
- Tech Scout
- Unparalleled Data Quality
- Higher Quality Content
- 60% Fewer Hallucinations
Browse by: Latest US Patents, China's latest patents, Technical Efficacy Thesaurus, Application Domain, Technology Topic, Popular Technical Reports.
© 2025 PatSnap. All rights reserved.Legal|Privacy policy|Modern Slavery Act Transparency Statement|Sitemap|About US| Contact US: help@patsnap.com