Catalytic converting method for improving petrol octane number
A catalytic conversion method and a technology for gasoline octane number, which are applied in directions such as naphtha catalytic reforming, can solve problems such as large loss of gasoline, and achieve the effects of increasing octane number, reducing sulfur content, and reducing olefins
- Summary
- Abstract
- Description
- Claims
- Application Information
AI Technical Summary
Problems solved by technology
Method used
Image
Examples
Embodiment 1
[0041] This example illustrates: the effect of catalytic upgrading of heavy gasoline of different fractions by adopting the method provided by the present invention.
[0042] The gasoline fractions G2 and G3 listed in Table 3 were used as raw materials, and the catalyst B listed in Table 2 was used to carry out the test in a small fluidized bed reactor operated by continuous reaction regeneration. The test procedure is briefly described as follows: inject the preheated gasoline fraction G2 or G3 into the fluidized bed reactor, and the reaction temperature is 450 ° C, the pressure at the top of the reactor is 0.2 MPa, and the weight hourly space velocity is 10 hours. -1 , the agent-oil ratio is 6, and the water-oil ratio is 0.05, and it contacts and reacts with the catalyst B with carbon; the reaction product, water vapor and the unborn catalyst are separated in the settler, and the reaction product is separated, and the unborn catalyst enters the stripping The hydrocarbon prod...
Embodiment 2
[0047] This example illustrates that the method provided by the invention is applicable to different types of catalytic cracking catalysts.
[0048] Using the gasoline G2 listed in Table 3 as raw material and using the three catalysts listed in Table 2, the test was carried out in a small fluidized bed reactor operated by continuous reaction regeneration. Concrete test procedure is identical with embodiment 1. The test conditions, test results and properties of gasoline products are listed in Table 5.
[0049] As can be seen from Table 5, after the process provided by the present invention, the yield of gasoline products is 91.32 to 91.88% by weight, and the total liquid yield is 96.62 to 97.47% by weight, and the gasoline research method octane number after upgrading can be improved 1.1 to 2.2 units, the motor octane number can be increased by 0.8 to 1.1 units. Therefore, different types of catalysts can be used to implement the present invention to obtain relatively ideal ...
Embodiment 3
[0051] This example shows that within the scope of the reaction conditions described in the present invention, the upgrading effect of the octane number of the heavy gasoline fraction is relatively ideal.
[0052] Using the gasoline fraction G2 in Table 3 as the raw material and using the catalyst B in Table 2, a catalytic upgrading test was carried out in a small fluidized bed reactor operated by continuous reaction regeneration. The main operating conditions are: the reaction temperature is 400-500°C, the pressure at the top of the reactor is 0.2 MPa, and the weight hourly space velocity is 5-20 hours -1 , The agent-oil ratio is 4-10. Concrete test procedure is identical with embodiment 1. The test conditions, test results and properties of gasoline products are listed in Table 6.
[0053] As can be seen from Table 6, after the process provided by the present invention, the yield of gasoline products is 91.02~91.82% by weight, the total liquid yield is 96.54~97.18% by weig...
PUM
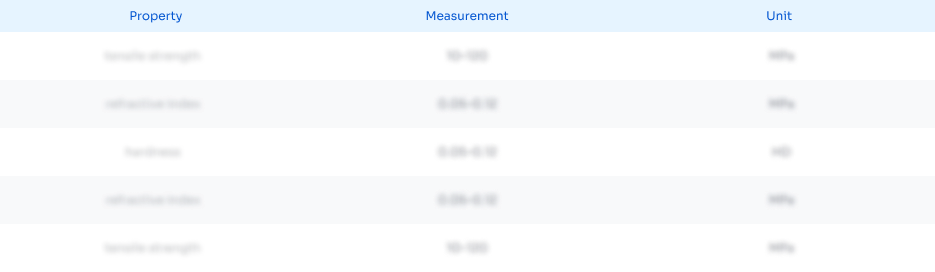
Abstract
Description
Claims
Application Information

- R&D
- Intellectual Property
- Life Sciences
- Materials
- Tech Scout
- Unparalleled Data Quality
- Higher Quality Content
- 60% Fewer Hallucinations
Browse by: Latest US Patents, China's latest patents, Technical Efficacy Thesaurus, Application Domain, Technology Topic, Popular Technical Reports.
© 2025 PatSnap. All rights reserved.Legal|Privacy policy|Modern Slavery Act Transparency Statement|Sitemap|About US| Contact US: help@patsnap.com