Apparatus and method for casting amorphous metal alloys in an adjustable low density atmosphere
A gas environment, metal casting technology, applied in the field of molten metal casting metal strip, can solve the problem of insufficient reduction of metal strip, and achieve the effects of reducing the formation and retention of bubbles, uniform finish, and uniform strip thickness distribution
- Summary
- Abstract
- Description
- Claims
- Application Information
AI Technical Summary
Problems solved by technology
Method used
Image
Examples
example
[0075] The effect of the inventive casting system on the strip thickness distribution during casting was investigated.
[0076] as per Figure 4 A burner was constructed as described in ~8 with six individually controllable gas valves, nozzles and combustion chambers, each approximately 2 inches wide. The burner is used in an attempt to control the ribbon thickness distribution in the ribbon dispersing section by adjusting the gas flow in the dispersing section without significantly affecting the other sections.
[0077] First, the airflow through all six nozzles was adjusted so that all nozzles supplied the same airflow (approximately 10 liters / minute per nozzle). System adjustments are made so that casting takes place as much as possible without changing the airflow in individually controllable areas. Thus obtaining the best possible casting. The x-ray device is configured to pass the width of the belt as the belt moves through the x-ray device. Therefore, all thickness ...
PUM
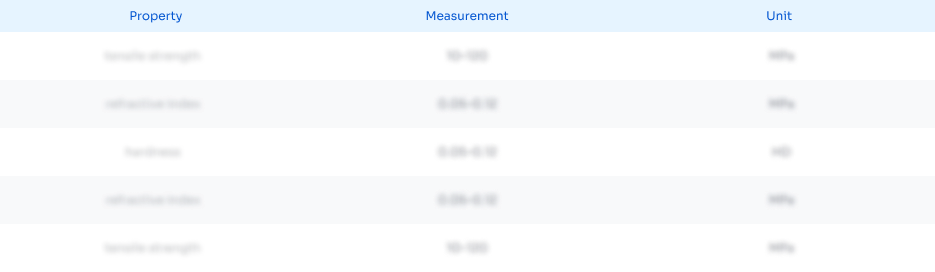
Abstract
Description
Claims
Application Information

- R&D
- Intellectual Property
- Life Sciences
- Materials
- Tech Scout
- Unparalleled Data Quality
- Higher Quality Content
- 60% Fewer Hallucinations
Browse by: Latest US Patents, China's latest patents, Technical Efficacy Thesaurus, Application Domain, Technology Topic, Popular Technical Reports.
© 2025 PatSnap. All rights reserved.Legal|Privacy policy|Modern Slavery Act Transparency Statement|Sitemap|About US| Contact US: help@patsnap.com