Semiconductor light-emitting device and its manufacturing method
一种发光元件、制造方法的技术,应用在半导体激光器、半导体激光器装置、光波导半导体的结构等方向,能够解决难以熔融大口径基板表面、发光波长不稳定、难以形成多个形状一致凹部等问题
- Summary
- Abstract
- Description
- Claims
- Application Information
AI Technical Summary
Problems solved by technology
Method used
Image
Examples
Embodiment approach 1
[0054] figure 2 It is a plan view showing the structure of the semiconductor light emitting element according to Embodiment 1 of the present invention. and image 3 Yes figure 2 The III-III line view, Figure 4 Yes figure 2 The IV-IV line view. In addition, the emission wavelength of the semiconductor light emitting element of this embodiment is 1.3 μm.
[0055] like Figure 2 to Figure 4 As shown, a stripe structure 10 is formed on an n-type InP substrate 1 . The stripe structure 10 is an n-type InP lower cladding layer 3 (thickness 100nm), an InGaAsP / InGaAsP quantum well active layer 4 (hereinafter referred to as the active layer 4 ), and a p-type InP upper cladding layer 5 (thickness 50nm). ) to form. Here, the active layer 4 is 5 pairs of In 0.9 Ga 0.1 As 0.2 P 0.8 Barrier layer (thickness 10nm, composition wavelength 1.1μm, lattice deformation 0%), In 0.9 Ga 0.1 As 0.5 P 0.5 A deformed quantum well structure composed of a well layer (thickness 4nm, quan...
Embodiment approach 2
[0081] In Embodiment 2, a semiconductor light-emitting element is shown in which there is a photonic crystal similar to Embodiment 1, but the period of the photonic crystal in the direction of the resonator is different from the period of the photonic crystal in the direction perpendicular to the direction of the resonator. .
[0082] Figure 8 It is a plan view showing the structure of the semiconductor light emitting element according to Embodiment 2 of the present invention. like Figure 8 As shown, the photonic crystal structure 2 is formed by arranging a plurality of recesses 9 in a rectangular lattice. Here, the period F1 of the recesses 9 in the resonator direction (interval between adjacent recesses 9 ) is longer than the period F2 of the recesses 9 in the direction perpendicular to the resonator direction. In addition, 13 in the figure represents a growth region when the p-type InP upper cladding layer is selectively grown as will be described later. In addition, ...
Embodiment approach 3
[0099] Embodiment 3 shows a semiconductor light emitting element in which leakage of naturally emitted light and induced emitted light in the direction of the resonator can be prevented by forming a reflective film that reflects light on the end surfaces of the stripe structure.
[0100] Figure 11 It is a figure showing the structure of the semiconductor light emitting element of Embodiment 3 of this invention, Figure 11 (a) is a plan view showing its structure, Figure 11 (b) is Figure 11 (a) A-A line view. like Figure 11 (a) and Figure 11 As shown in (b), an insulator multilayer thin film 11 made of alumina and titania is formed on both end surfaces of the stripe structure 10 . In addition, the other configurations of the semiconductor light-emitting element of this embodiment are the same as those of Embodiment 1, so the same reference numerals are assigned and descriptions thereof are omitted.
[0101] Hereinafter, a method of manufacturing the semiconductor lig...
PUM
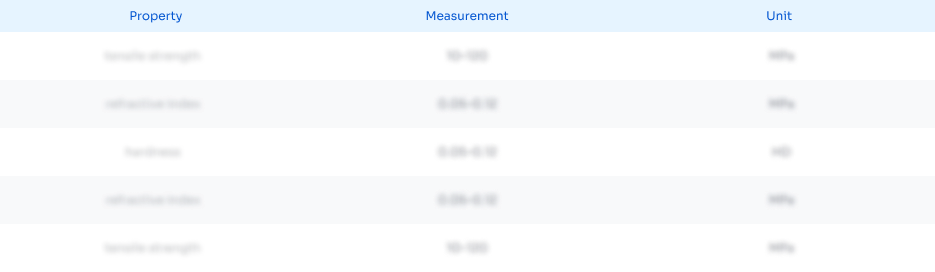
Abstract
Description
Claims
Application Information

- Generate Ideas
- Intellectual Property
- Life Sciences
- Materials
- Tech Scout
- Unparalleled Data Quality
- Higher Quality Content
- 60% Fewer Hallucinations
Browse by: Latest US Patents, China's latest patents, Technical Efficacy Thesaurus, Application Domain, Technology Topic, Popular Technical Reports.
© 2025 PatSnap. All rights reserved.Legal|Privacy policy|Modern Slavery Act Transparency Statement|Sitemap|About US| Contact US: help@patsnap.com