Rolling and cogging method for OCr17Ni4Cu4Nb casting ingots
A production method and ingot casting technology, applied in the direction of metal rolling, etc., can solve the problems of long production cycle and low metal billet rate, and achieve the effects of shortening the production cycle, high metal billet rate, and reducing metallurgical manufacturing costs
- Summary
- Abstract
- Description
- Claims
- Application Information
AI Technical Summary
Problems solved by technology
Method used
Image
Examples
Embodiment Construction
[0020] specific implementation plan
[0021] A certain iron and steel company implements the patent of the invention, adopts a soaking furnace to heat electroslag ingots (ingot weight 1.5-2.8 tons, 2.3 tons) + preliminary rolling mill (Φ800 rolling mill) hot-processed billet, and produces 0Cr17Ni4Cu4Nb steel billet (180 square meters mm, 220 square mm). During the first fire rolling of the blooming mill, the electroslag ingot is heated by the soaking furnace: (A) the electroslag ingot (single weight 2 tons, 2.3 tons) is hot sent to the soaking furnace, the temperature of the steel ingot is 700°C, and the temperature is kept for 0.5 hours ; (B) heat up to 900°C at a rate of 50-60°C / h, and keep warm for 2 hours; (C) heat up to 1190°C at a speed of 100°C / h; (D) keep warm at 1190°C for 4 hours, and keep the steel ingot Turn over one by one to reduce the temperature difference between the positive and negative sides of the steel ingot; (E) The temperature difference between the ne...
PUM
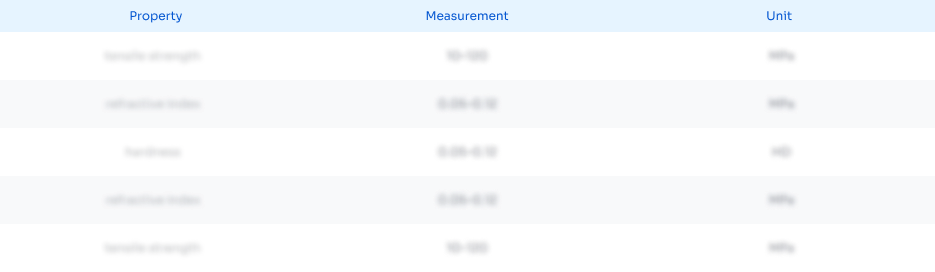
Abstract
Description
Claims
Application Information

- R&D
- Intellectual Property
- Life Sciences
- Materials
- Tech Scout
- Unparalleled Data Quality
- Higher Quality Content
- 60% Fewer Hallucinations
Browse by: Latest US Patents, China's latest patents, Technical Efficacy Thesaurus, Application Domain, Technology Topic, Popular Technical Reports.
© 2025 PatSnap. All rights reserved.Legal|Privacy policy|Modern Slavery Act Transparency Statement|Sitemap|About US| Contact US: help@patsnap.com