Method for forming osteolith class layer on surface of calcium phosphate ceramics
A technology of calcium phosphate ceramics and apatite, applied in the direction of bone implants, etc., can solve the problems of uneven distribution, high process cost, complicated device, etc., and achieve the effect of fast deposition rate, high surface activity, and growth promotion.
- Summary
- Abstract
- Description
- Claims
- Application Information
AI Technical Summary
Problems solved by technology
Method used
Examples
Embodiment 1
[0017] (1) Clean the porous calcium phosphate ceramics prepared by artificial synthesis in deionized water or distilled water, and dry them at 80°C;
[0018] (2) prepare 12 moles of sodium hydroxide aqueous solution with analytically pure sodium hydroxide reagent and deionized water or distilled water;
[0019] (3) Add 24.00 grams of sodium chloride (NaCl) and sodium bicarbonate (NaHCO) to 1000 ml of deionized water or distilled water 3 ) 1.01 grams, potassium chloride (KCl) 0.69 grams, dipotassium hydrogen phosphate (K 2 HPO 4 ·3H 2 O) 0.69 g, magnesium chloride (MgCl 2 ·6H 2 O) 0.93 g, calcium chloride (CaCl 2 2H 2 O) 0.84 grams, sodium sulfate (Na 2 SO 4 ) 0.21 g, Tris (CH 2 Oh) 3 CNH 2 ) 18.18 grams, prepare simulated body fluid, and adjust the pH value of simulated body fluid to 7.2~7.4 with 1 mole hydrochloric acid solution, prepare simulated body fluid;
[0020] (4) Place the calcium phosphate ceramics cleaned in step (1) in a glass container, add the 12 mol...
Embodiment 2
[0025] (1) Clean the porous calcium phosphate ceramics prepared by the coral conversion method in deionized water or distilled water, and dry at 90°C;
[0026] (2) Prepare 8 moles of sodium hydroxide aqueous solution with analytically pure sodium hydroxide reagent and deionized water or distilled water;
[0027] (3) Add 12.00 grams of sodium chloride (NaCl) and sodium bicarbonate (NaHCO) to 1000 ml of deionized water or distilled water 3 ) 0.525 grams, potassium chloride (KCl) 0.345 grams, dipotassium hydrogen phosphate (K 2 HPO 4 ·3H 2 O) 0.345 grams, magnesium chloride (MgCl 2 ·6H 2 O) 0.465 grams, calcium chloride (CaCl 2 2H 2 O) 0.42 grams, sodium sulfate (Na 2 SO 4 ) 0.105 g, Tris (CH 2 Oh) 3 CNH 2 ) 9.09 grams to prepare a simulated body fluid, and adjust the pH value of the simulated body fluid to 7.2 to 7.4 with 1 mole of hydrochloric acid solution; prepare the simulated body fluid;
[0028] (4) Place the calcium phosphate ceramics cleaned in step (1) in a ...
Embodiment 3
[0033] (1) Clean the porous calcium phosphate ceramics prepared by the natural bone calcination method in deionized water or distilled water, and dry them at 100°C;
[0034] (2) Prepare 1 mole of sodium hydroxide aqueous solution with analytically pure sodium hydroxide reagent and deionized water or distilled water;
[0035] (3) Add 8.00 grams of sodium chloride (NaCl) and sodium bicarbonate (NaHCO) to 1000 ml of deionized water or distilled water 3 ) 0.35 grams, potassium chloride (KCl) 0.23 grams, dipotassium hydrogen phosphate (K 2 HPO 4 ·3H 2 O) 0.23 g, magnesium chloride (MgCl2 ·6H 2 O) 0.31 g, calcium chloride (CaCl 2 2H 2 O) 0.28g grams, sodium sulfate (Na 2 SO 4 ) 0.07 g, Tris (CH 2 Oh) 3 CNH 2 ) 6.06 grams, prepare simulated body fluid, and adjust the pH value of simulated body fluid to 7.2~7.4 with 1 mole hydrochloric acid solution, prepare simulated body fluid;
[0036] (4) Place the calcium phosphate ceramics cleaned in step (1) in a glass container, add...
PUM
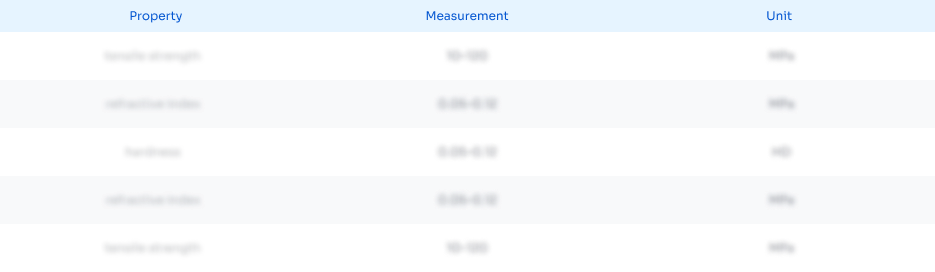
Abstract
Description
Claims
Application Information

- R&D
- Intellectual Property
- Life Sciences
- Materials
- Tech Scout
- Unparalleled Data Quality
- Higher Quality Content
- 60% Fewer Hallucinations
Browse by: Latest US Patents, China's latest patents, Technical Efficacy Thesaurus, Application Domain, Technology Topic, Popular Technical Reports.
© 2025 PatSnap. All rights reserved.Legal|Privacy policy|Modern Slavery Act Transparency Statement|Sitemap|About US| Contact US: help@patsnap.com