Synthesis method of magnesium hydroxide nano pipe
A technology of magnesium hydroxide and a synthesis method, which is applied in the field of synthesis of magnesium hydroxide nanotubes, can solve problems such as unfavorable large-scale industrial production, complicated reaction process, and reduced product purity, and achieve easy control of production conditions, low cost, The effect of high product purity
- Summary
- Abstract
- Description
- Claims
- Application Information
AI Technical Summary
Problems solved by technology
Method used
Image
Examples
Embodiment 1
[0014] Weigh 0.001mol of magnesium chloride and place it in a beaker, add 20ml of deionized water, stir to dissolve it, then quickly add 10ml of 5M ammonia solution, continue stirring for 10 minutes, and then centrifugally wash the obtained precipitate until the pH of the solution is 7 , redisperse the precipitate in a mixed solvent of 20ml of methanol and water, then add 0.3g of potassium chloride as a mineralizer and stir to dissolve it, and transfer the stirred and dissolved mixture into a closed stainless steel reactor, at 240°C The reaction was carried out under low temperature for 18 hours. After the reaction was complete, it was cooled to normal temperature, and then the obtained product was washed with deionized water and dried at 50°C to obtain the product. The product was identified as magnesium hydroxide by X-ray powder diffraction; the morphology of the product was detected by TEM and SEM electron microscopy.
Embodiment 2
[0016] Weigh 0.001mol of magnesium nitrate and place it in a beaker, add 20ml of deionized water, stir to dissolve it, then quickly add 10ml of 5M ammonia solution, continue stirring for 10 minutes, and then centrifugally wash the obtained precipitate until the pH of the solution is 7. Redisperse the precipitate in a mixed solvent of 20ml of methanol and water, then add 0.4g of sodium sulfate as a mineralizer and stir to dissolve it, and transfer the stirred and dissolved mixture into a closed stainless steel reactor, at 220°C The reaction was carried out under low temperature for 22 hours. After the reaction was complete, it was cooled to room temperature, and then the obtained product was washed with deionized water and dried at 60°C to obtain the product. The product was identified as magnesium hydroxide by X-ray powder diffraction; the morphology of the product was detected by TEM and SEM electron microscopy.
Embodiment 3
[0018] Weigh 0.001mol of magnesium chloride and place it in a beaker, add 20ml of deionized water, stir to dissolve it, then quickly add 10ml of 5M ammonia solution, continue stirring for 10 minutes, and then centrifugally wash the obtained precipitate until the pH of the solution is 7 , redisperse the precipitate in a mixed solvent of 20ml of methanol and water, then add a mixture of 0.2g of sodium chloride and 0.2g of potassium nitrate as a mineralizer and stir to dissolve it, and move the stirred and dissolved mixture into a stainless steel closed reaction React in a container at 240°C for 20 hours, cool to normal temperature after the reaction is complete, then wash the obtained product with deionized water, and dry at 60°C to obtain the product. The product was identified as magnesium hydroxide by X-ray powder diffraction; the morphology of the product was detected by TEM and SEM electron microscopy.
PUM
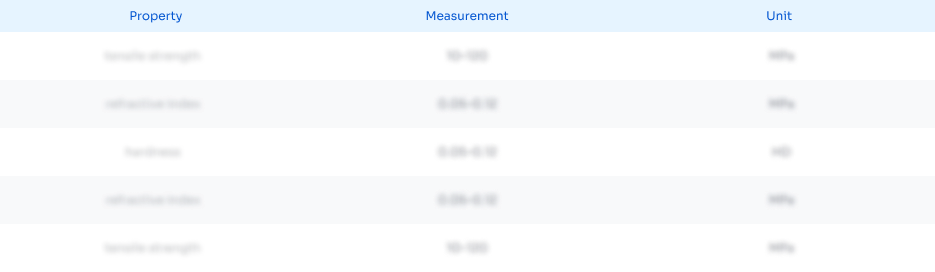
Abstract
Description
Claims
Application Information

- R&D
- Intellectual Property
- Life Sciences
- Materials
- Tech Scout
- Unparalleled Data Quality
- Higher Quality Content
- 60% Fewer Hallucinations
Browse by: Latest US Patents, China's latest patents, Technical Efficacy Thesaurus, Application Domain, Technology Topic, Popular Technical Reports.
© 2025 PatSnap. All rights reserved.Legal|Privacy policy|Modern Slavery Act Transparency Statement|Sitemap|About US| Contact US: help@patsnap.com