Production method of pressing casting fishing gear
A production method and technology of fishing gear, applied in fishing, animal husbandry, application, etc., can solve problems such as insufficient product quality density, low production efficiency, exhaust, etc., achieve good product quality and density, speed up die-casting, and avoid defects point effect
- Summary
- Abstract
- Description
- Claims
- Application Information
AI Technical Summary
Problems solved by technology
Method used
Image
Examples
Embodiment Construction
[0007] See attached figure 1 As shown, the present invention is a manufacturing method of die-casting processing fishing gear, which mainly includes the steps of mold closing, soup feeding, injection into the mold, cooling, mold opening and sampling, turning and surface treatment in succession. A vacuuming process is added synchronously to the implementation process of the steps.
[0008] The two halves of the mold are closed to form a hollow mold cavity. The soup is delivered to the heat preservation furnace through the corresponding spoon to transport the aluminum alloy material that has been dissolved at high temperature in advance, and then injected into the mold. The dissolved aluminum alloy material enters the mold through the material tube. Molding in the cavity, and at this time, the vacuum device connected to the mold is started synchronously to evacuate, and the residual air in the cavity is drawn out of the mold in time, so that a vacuum state is formed in the cavit...
PUM
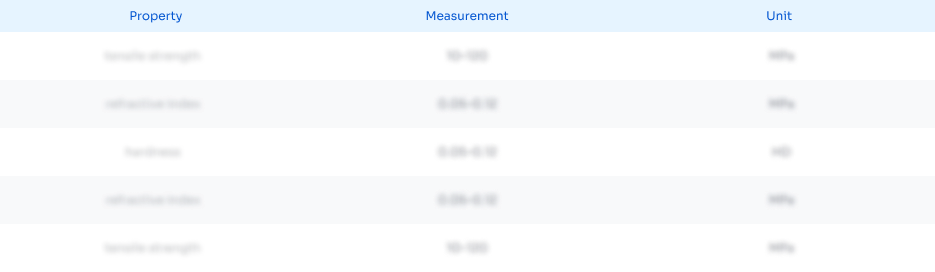
Abstract
Description
Claims
Application Information

- Generate Ideas
- Intellectual Property
- Life Sciences
- Materials
- Tech Scout
- Unparalleled Data Quality
- Higher Quality Content
- 60% Fewer Hallucinations
Browse by: Latest US Patents, China's latest patents, Technical Efficacy Thesaurus, Application Domain, Technology Topic, Popular Technical Reports.
© 2025 PatSnap. All rights reserved.Legal|Privacy policy|Modern Slavery Act Transparency Statement|Sitemap|About US| Contact US: help@patsnap.com