Welding method for heat radiating fin of heat exchanger and equipment thereof
A heat dissipation fin and heat exchanger technology, applied in welding equipment, arc welding equipment, heat exchange equipment, etc., can solve the problems of loose fins, loss of heat conduction and heat exchange function, poor heat conduction and heat dissipation, etc., and improve heat conduction and heat exchange. Thermal performance, welding effect is good, and the effect of prolonging service life
- Summary
- Abstract
- Description
- Claims
- Application Information
AI Technical Summary
Problems solved by technology
Method used
Image
Examples
Embodiment Construction
[0015] See Figure 1-3 , heat exchanger cooling fin welding equipment is as follows:
[0016] Set a C618K-1500 type lathe 10 refitted by stepless speed regulation, assemble the follower frame 2 on the tool rest 1, the follower frame 2 has two half-arc parts 2.1, 2.2, and one half-arc part 2.1 is connected with Sliding shaft 12, sliding shaft 12 is slidably inserted in the sliding sleeve 11 on the tool rest 1. One side of the two semi-arc parts 2.1, 2.2 is hinged by a hinge shaft 13 to form an openable and closable circular follower frame, and a locking part is assembled on the side that can be opened and closed. The locking part is provided with a jacket 18, and a spring 17 is housed in the jacket 18 , the connecting screw 19 passes therethrough, and the bottom of the connecting screw 19 penetrates the gap on the connecting edge of the half-arc part 2.2, and its upper end is hinged with the trigger 16 of the arc-shaped end. When the trigger 16 is upright, the spring 17 is co...
PUM
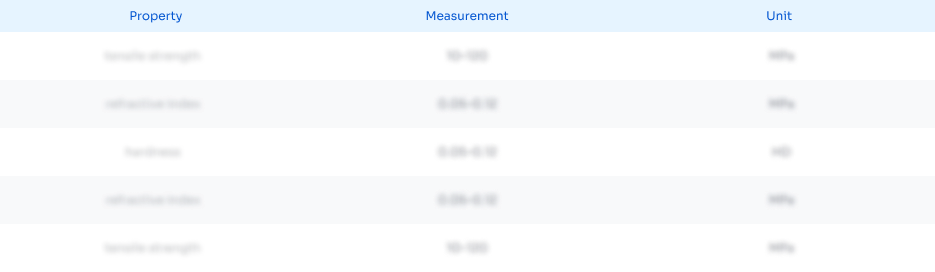
Abstract
Description
Claims
Application Information

- Generate Ideas
- Intellectual Property
- Life Sciences
- Materials
- Tech Scout
- Unparalleled Data Quality
- Higher Quality Content
- 60% Fewer Hallucinations
Browse by: Latest US Patents, China's latest patents, Technical Efficacy Thesaurus, Application Domain, Technology Topic, Popular Technical Reports.
© 2025 PatSnap. All rights reserved.Legal|Privacy policy|Modern Slavery Act Transparency Statement|Sitemap|About US| Contact US: help@patsnap.com