Manufacture of micro syringe array
A manufacturing method and technology of needles, applied in the direction of hypodermic injection devices, etc., can solve the problems of complicated production process steps and inability to achieve mass production
- Summary
- Abstract
- Description
- Claims
- Application Information
AI Technical Summary
Problems solved by technology
Method used
Image
Examples
Embodiment Construction
[0042] 1. Fabrication of microneedle arrays by metal plating
[0043] see Figure 1A to Figure 1H , the manufacturing method of the microneedle array provided by the first preferred embodiment of the present invention is accomplished through the following steps:
[0044] First, a protective layer 110 (such as nitride (Si3N4)) is laid on the upper and lower surfaces of a silicon wafer 100, such as Figure 1A , Figure 1B Lay the photoresist, expose and develop to define the area to be etched, and etch the protective layer 110 to obtain the area to be wet etched 111, and then apply wet etching to the local silicon wafer 110 exposed in the area to be wet etched 111, because the silicon wafer 100 is exposed in the wet etching area 111. The characteristics of anisotropic etching exhibited during etching can form a recessed region 101 with a slope geometry, such as Figure 1C , and then the protective layer 110 on the bottom side also defines the region 112 to be dry etched by lit...
PUM
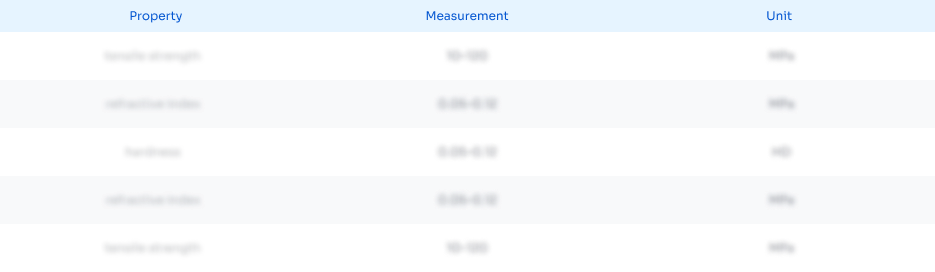
Abstract
Description
Claims
Application Information

- R&D Engineer
- R&D Manager
- IP Professional
- Industry Leading Data Capabilities
- Powerful AI technology
- Patent DNA Extraction
Browse by: Latest US Patents, China's latest patents, Technical Efficacy Thesaurus, Application Domain, Technology Topic, Popular Technical Reports.
© 2024 PatSnap. All rights reserved.Legal|Privacy policy|Modern Slavery Act Transparency Statement|Sitemap|About US| Contact US: help@patsnap.com