Well killing method using solid water particles as kill fluid
A solid water and kill fluid technology, applied in wellbore/well components, earthmoving, sealing/packing, etc., can solve problems such as short stabilization time, difficult blowout accidents, corrosion of downhole oil and gas casings, etc. Good performance and good killing effect
- Summary
- Abstract
- Description
- Claims
- Application Information
AI Technical Summary
Problems solved by technology
Method used
Examples
Embodiment 1
[0022] 1. Prepare the designed volume of clean water for well killing;
[0023] 2. Add corrosion inhibitors, drainage aids, clay stabilizers and other agents used to protect oil and gas wells (these agents are commonly used in drilling and killing wells);
[0024] 3. Add glycerin, its adding ratio is 0.5% of water; add sodium thiosulfate, its adding ratio is 0.1% of water;
[0025] 4. Add acrylic acid and sodium acrylate copolymer, the proportion of which is 0.5% of water, and stir well to form solid water particles;
[0026] 5. Use mud pump or fracturing truck to press solid water particles into the wellbore through positive circulation or reverse circulation;
[0027] 6. Cycle for one week after killing the well, observe for 48 hours, and open the wellhead for underground construction after the well is stable;
[0028] 7. Use methods such as suction or gas lift to discharge the solid water particles in the wellbore and put it into production.
Embodiment 2
[0030] 1. Prepare the designed amount of brine for well killing;
[0031] 2. Add corrosion inhibitors, drainage aids, clay stabilizers and other agents used to protect oil and gas wells (these agents are commonly used in drilling and killing wells);
[0032] 3. Add methacrylamine, its addition ratio is 1% of water; add sodium sulfite, its addition ratio is 0.2% of water;
[0033] 4. Add starch-polyacrylonitrile, the proportion of which is 2% of water, and stir well to form solid water particles;
[0034] 5. Use mud pump or fracturing truck to press solid water particles into the wellbore through positive circulation or reverse circulation;
[0035] 6. Cycle for one week after killing the well, observe for 48 hours, and open the wellhead for underground construction after the well is stable;
[0036] 7. Use methods such as suction or gas lift to discharge the solid water particles in the wellbore and put it into production.
Embodiment 3
[0038] 1. Prepare the designed amount of brine for well killing;
[0039] 2. Add corrosion inhibitors, drainage aids, clay stabilizers and other agents used to protect oil and gas wells (these agents are commonly used in drilling and killing wells);
[0040] 3. Adding formaldehyde, its addition ratio is 0.6% of water; adding sodium metabisulfite, its addition ratio is 0.15% of water;
[0041] 4. Add starch-polyacrylic acid, the proportion of which is 3% of water, and stir well to form solid water particles;
[0042] 5. Use mud pump or fracturing truck to press solid water particles into the wellbore through positive circulation or reverse circulation;
[0043] 6. Cycle for one week after killing the well, observe for 48 hours, and open the wellhead for underground construction after the well is stable;
[0044] 7. Use methods such as suction or gas lift to discharge the solid water particles in the wellbore and put it into production.
PUM
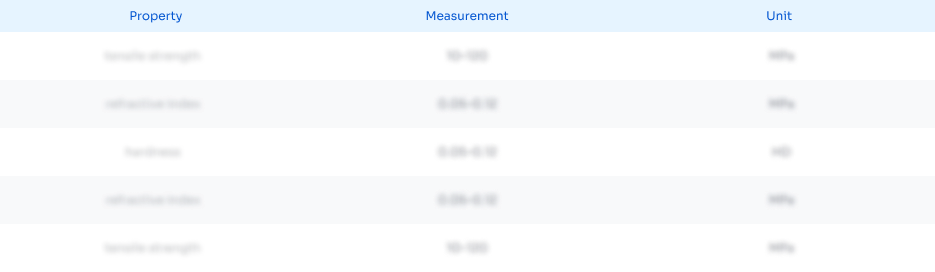
Abstract
Description
Claims
Application Information

- R&D
- Intellectual Property
- Life Sciences
- Materials
- Tech Scout
- Unparalleled Data Quality
- Higher Quality Content
- 60% Fewer Hallucinations
Browse by: Latest US Patents, China's latest patents, Technical Efficacy Thesaurus, Application Domain, Technology Topic, Popular Technical Reports.
© 2025 PatSnap. All rights reserved.Legal|Privacy policy|Modern Slavery Act Transparency Statement|Sitemap|About US| Contact US: help@patsnap.com