Honing method and honing equipment
A technology of honing and equipment, which is applied in the direction of honing machine tools, metal processing equipment, manufacturing tools, etc., can solve the problems of prolonging machining time and increasing manufacturing costs, and achieve the effects of avoiding machining time, reducing plastic flow, and avoiding prolongation
- Summary
- Abstract
- Description
- Claims
- Application Information
AI Technical Summary
Problems solved by technology
Method used
Image
Examples
Embodiment Construction
[0029] Hereinafter, embodiments of the present invention will be described with reference to the accompanying drawings.
[0030] figure 1 A honing method in one embodiment of the present invention is shown. exist figure 1 In , reference numeral 101 denotes a rough honing step area of the honing method, and 103 denotes a fine honing step area thereof. Also, between the rough honing step area 101 and the fine honing step area 103, an idle step area 102 for leaving the workpiece as it is for a predetermined time ("stand alone time" or "leave time") is provided. ). These step areas are set on the same processing line (working line). An engine cylinder block 11 having a cylindrical inner surface is carried as one workpiece on the processing line in the order of a rough honing step area 101 , an idle step area 102 , and a finish honing step area 103 .
[0031] Such as figure 1 As shown in the rough honing step of , the honing head 15 is inserted into the cylinder bore 13 ...
PUM
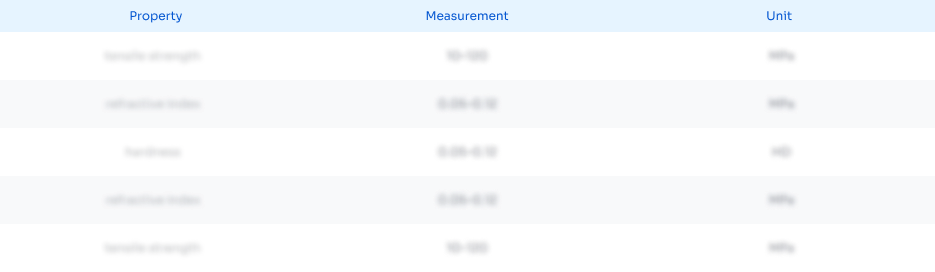
Abstract
Description
Claims
Application Information

- R&D Engineer
- R&D Manager
- IP Professional
- Industry Leading Data Capabilities
- Powerful AI technology
- Patent DNA Extraction
Browse by: Latest US Patents, China's latest patents, Technical Efficacy Thesaurus, Application Domain, Technology Topic, Popular Technical Reports.
© 2024 PatSnap. All rights reserved.Legal|Privacy policy|Modern Slavery Act Transparency Statement|Sitemap|About US| Contact US: help@patsnap.com