Process for preparing flexible polyurethane foam plastic
A technology of soft polyurethane and foam plastics, applied in the field of soft polyurethane foam plastics, can solve problems such as the decline in mechanical properties of products, and achieve the effects of reduced catalyst consumption, cost reduction, and comfortable hand feeling
- Summary
- Abstract
- Description
- Claims
- Application Information
AI Technical Summary
Problems solved by technology
Method used
Examples
Embodiment 1
[0022] 1. Catalyst preparation: use diethylene glycol dimethyl ether as an organic ligand to prepare a zinc hexacyanocobaltate / zinc sulfate (DMC) composite catalyst improved with zinc sulfate;
[0023] (1) Solution preparation
[0024] Solution A: Dissolve 15g of potassium hexacyanocobaltate in 270ml of deionized water;
[0025] Solution B: Dissolve 45g of zinc chloride in 75ml of deionized water;
[0026] Solution C: a mixture of 180ml diethylene glycol dimethyl ether and 180ml deionized water;
[0027] (2) After mixing solution A and solution B under high-speed stirring, immediately add solution C to obtain a milky white suspension, continue stirring for 30 minutes, and separate the solid matter by filtration;
[0028] (3) Slurry the solid with a mixture solution containing zinc sulfate, stir for 20min, and filter;
[0029] Slurry composition: 105ml diethylene glycol dimethyl ether + 45ml deionized water + 12g zinc sulfate
[0030] (Potassium zinc hexacyanoco...
Embodiment 2
[0042] Embodiment two: (ultra-low density 8g / cm 3 Polyurethane flexible foam)
[0043] 1, the preparation of catalyst is with embodiment one;
[0044] 2, low unsaturation polyether polyol is prepared with embodiment one;
[0045] 3. Preparation of polyol components: low unsaturation polyether polyol, water, physical foaming agent, catalyst, surfactant, filler by weight ratio: low unsaturation polyether polyol: water: dichloro Methane: A-33 (dipropylene glycol solution of 33% WT triethylenediamine): dibutyltin dilaurate: surfactant (L-580, U.S. high Schmitt company product): polymer polyol ( TPOP93-28, produced by Tianjin No. 3 Petrochemical Plant): talcum powder (300 mesh) = 60: 8.5: 35: 0.6: 1.2: 3.5: 40: 45, keep the temperature at 30°C, and mix well in the container to obtain polyol Component;
[0046] 4. Isocyanate component: a mixture of 2,4-toluene diisocyanate and 2,6-toluene diisocyanate, the isomerization ratio is 80 / 20 (i.e. TDI-80) 103.5 parts, the temperature i...
Embodiment 3
[0054] 1, catalyst preparation, with embodiment one;
[0055] 2, low unsaturation polyether polyol is prepared with embodiment one;
[0056] 3. Preparation of polyol components: low unsaturation polyether polyol, water, catalyst, surfactant by weight ratio: low unsaturation polyether polyol: water: A-33 (33% WT Sanethylene dipropylene glycol solution of base diamine): dibutyltin dilaurate: surfactant (L-580, U.S. High Schmitt company product)=100: 4.0: 0.12: 0.12: 0.8, maintain temperature 35 ℃, in Mix well in the container to obtain the polyol component;
[0057] 4. Isocyanate component: a mixture of 2,4-toluene diisocyanate and 2,6-toluene diisocyanate, the isomerization ratio is 80 / 20 (i.e. TDI-80) 49 parts, the temperature is kept within 35°C for standby;
[0058] 5. Fully mix the isocyanate component and the polyol component at a temperature of 35°C, pour, foam, and post-cure to obtain the product. The test results are shown in Table 2.
PUM
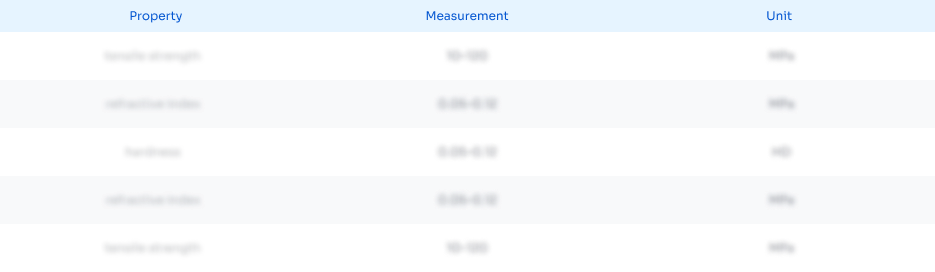
Abstract
Description
Claims
Application Information

- R&D
- Intellectual Property
- Life Sciences
- Materials
- Tech Scout
- Unparalleled Data Quality
- Higher Quality Content
- 60% Fewer Hallucinations
Browse by: Latest US Patents, China's latest patents, Technical Efficacy Thesaurus, Application Domain, Technology Topic, Popular Technical Reports.
© 2025 PatSnap. All rights reserved.Legal|Privacy policy|Modern Slavery Act Transparency Statement|Sitemap|About US| Contact US: help@patsnap.com