Method for making modified film superpressure mould releasing paper
A manufacturing method and technology of release paper, which can be applied in chemical instruments and methods, surface covering paper, paper/cardboard layered products, etc., and can solve the problems of shrinking contact surface, uneven sticking surface, and reduced sticking strength.
- Summary
- Abstract
- Description
- Claims
- Application Information
AI Technical Summary
Problems solved by technology
Method used
Examples
Embodiment Construction
[0007] Embodiments of the present invention are further described in detail below.
[0008] The implementation of the manufacturing method of the denatured film super-pressure release paper of the present invention uses reel white kraft paper as the main material, and the equipment includes a super calender, an unwinding paper stand, a two-color printing machine, an extruder, a cooling roll, and a slitting machine , winding paper frame and automatic tension control system, the super calender is composed of main frame, roller, pressurizing device, roll unwinding device, lifting platform, driving and electric transmission and other components, the two-color The printing machine is composed of corona treatment mechanism, deviation correction mechanism, primary printing, secondary printing, printing motor, roller and hot air drying system.
[0009] The specific operation steps are as follows:
[0010] 1. First, put the reel of white kraft paper into the paper unloading device of ...
PUM
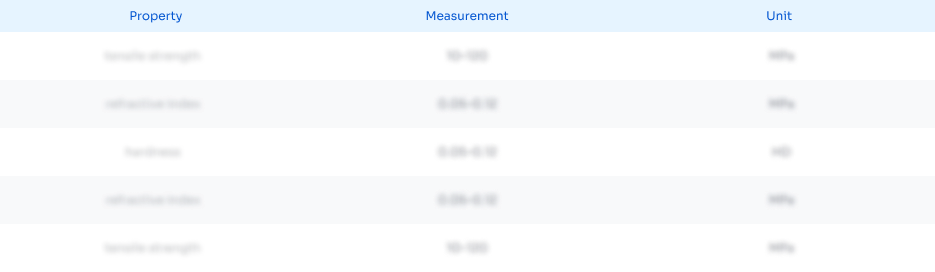
Abstract
Description
Claims
Application Information

- R&D
- Intellectual Property
- Life Sciences
- Materials
- Tech Scout
- Unparalleled Data Quality
- Higher Quality Content
- 60% Fewer Hallucinations
Browse by: Latest US Patents, China's latest patents, Technical Efficacy Thesaurus, Application Domain, Technology Topic, Popular Technical Reports.
© 2025 PatSnap. All rights reserved.Legal|Privacy policy|Modern Slavery Act Transparency Statement|Sitemap|About US| Contact US: help@patsnap.com