Prepn process of liquid polymerized ferric sulfate by means of oxidizing catalyst
A technology for polymerizing ferric sulfate and oxidation catalyst, applied in physical/chemical process catalysts, ferric sulfate, chemical instruments and methods, etc., can solve the problems of increasing drying energy consumption, prolonging drying time, increasing production cost, etc., and saving electricity and energy consumption, speed up the reaction, reduce drying energy consumption
- Summary
- Abstract
- Description
- Claims
- Application Information
AI Technical Summary
Problems solved by technology
Method used
Examples
Embodiment 1
[0030] Put ferrous sulfate, water, sulfuric acid, sodium chlorate and potassium permanganate into the reaction kettle one by one, stir thoroughly for 7-10 minutes, and it is ready. The ratio of the above raw materials is:
[0031] Ferrous sulfate 72%, sulfuric acid 6.0%, sodium chlorate 3.8%, potassium permanganate 1%, and the rest is water.
Embodiment 2
[0033] Put ferrous sulfate, water, sulfuric acid, sodium chlorate and potassium permanganate into the reaction kettle one by one, stir thoroughly for 7-10 minutes, and it is ready. The ratio of the above raw materials is:
[0034] 60% ferrous sulfate, 5.6% sulfuric acid, 3.0% sodium chlorate, 1% potassium permanganate, and the rest is water.
Embodiment 3
[0036] Put ferrous sulfate, water, sulfuric acid, sodium chlorate and potassium permanganate into the reaction kettle one by one, stir thoroughly for 7-10 minutes, and it is ready. The ratio of the above raw materials is:
[0037] Ferrous sulfate 75%, sulfuric acid 8.0%, sodium chlorate 3.8%, potassium permanganate 1%, and the rest is water.
PUM
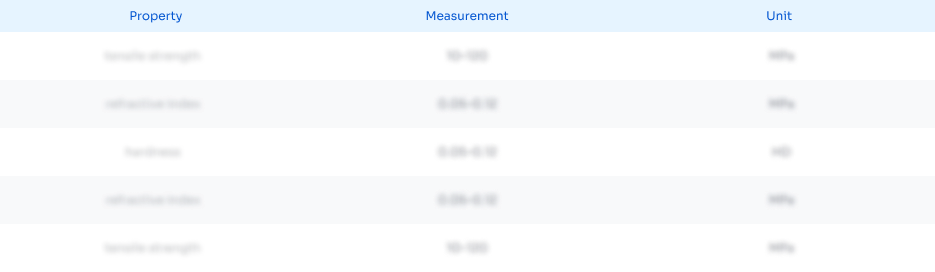
Abstract
Description
Claims
Application Information

- Generate Ideas
- Intellectual Property
- Life Sciences
- Materials
- Tech Scout
- Unparalleled Data Quality
- Higher Quality Content
- 60% Fewer Hallucinations
Browse by: Latest US Patents, China's latest patents, Technical Efficacy Thesaurus, Application Domain, Technology Topic, Popular Technical Reports.
© 2025 PatSnap. All rights reserved.Legal|Privacy policy|Modern Slavery Act Transparency Statement|Sitemap|About US| Contact US: help@patsnap.com