Method for producing ethyl phosphate with high purity
A technology for the production of triethyl phosphate, applied in the direction of phosphorus organic compounds, can solve the problems of increased alcohol consumption, increased production cost, incomplete reaction, etc., and achieve the effect of reducing consumption, reducing equipment investment, and complete reaction
- Summary
- Abstract
- Description
- Claims
- Application Information
AI Technical Summary
Problems solved by technology
Method used
Examples
Embodiment 1
[0014] a. Esterification reaction, put 30 kg of absolute ethanol into a 1000 liter reactor, start stirring, and inject cooling liquid ice salt water into the jacket of the reactor, and when the temperature in the reactor drops to 15°C, start Phosphorus oxychloride is added dropwise, and the reaction temperature is controlled by the rate of addition during the whole dropping process. The reaction temperature is maintained at 25°C. The time for dropping phosphorus oxychloride is greater than or equal to 1.5 hours until the ratio of phosphorus oxychloride to absolute ethanol reaches Up to 1:7, the unit is molar concentration. After dropping phosphorus oxychloride into the reactor, continue to keep the temperature at 25°C to carry out the deepening reaction for 2 hours. The vacuum degree in the reaction kettle is limited to the dropwise addition of phosphorus oxychloride, generally 0.06 MPa.
[0015] b, dealcoholization, the deepening reaction is completed, the material is transfe...
Embodiment 2
[0020] The difference between embodiment two and embodiment one is that the temperature that begins to drop phosphorus oxychloride in esterification reaction a is 13 ℃, and the reaction temperature used is 20 ℃, and the time of deepening reaction is 2.5 hours; The dealcoholization time is 1 hour; when neutralizing, the PH value is 6, and after stopping adding soda ash, continue to stir for 8 minutes; when distilling, the initial distillation time is 2 hours, and during the second distillation, remove the low boiler for the first time The temperature is 85°C.
Embodiment 3
[0022] The difference between embodiment three and embodiment one is that the temperature that begins to drop phosphorus oxychloride in esterification reaction a is 17 ℃, and the reaction temperature used is 30 ℃, and the time of deepening reaction is 1.5 hours; The dealcoholization time is 1.5 hours; when neutralizing, the pH value is 7, after stopping adding soda ash, continue to stir for 12 minutes; when distilling, the initial distillation time is 3 hours
[0023] During the second distillation, the temperature for removing the low boilers for the first time is 95°C.
PUM
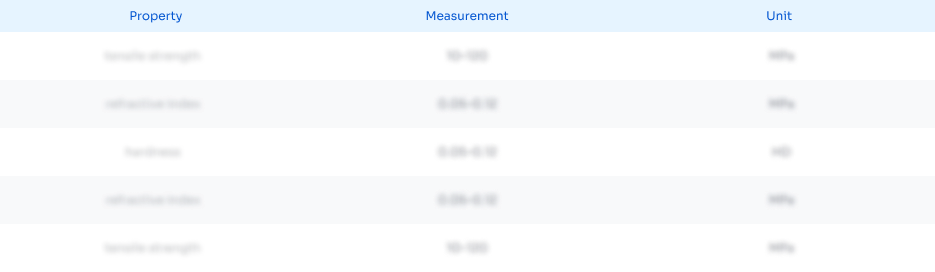
Abstract
Description
Claims
Application Information

- R&D
- Intellectual Property
- Life Sciences
- Materials
- Tech Scout
- Unparalleled Data Quality
- Higher Quality Content
- 60% Fewer Hallucinations
Browse by: Latest US Patents, China's latest patents, Technical Efficacy Thesaurus, Application Domain, Technology Topic, Popular Technical Reports.
© 2025 PatSnap. All rights reserved.Legal|Privacy policy|Modern Slavery Act Transparency Statement|Sitemap|About US| Contact US: help@patsnap.com