Layered decoupling coal-burning technology and mechanical layered decoupling furnace
A combustion technology and combustion furnace technology, which is applied in the field of mechanical layered decoupling combustion furnaces, can solve the problems of restricted use, increased CO and soot emissions, and increased smoke loss, so as to improve boiler combustion efficiency and reduce pollution. The effect of reducing the emission of pollutants and reducing combustion losses
- Summary
- Abstract
- Description
- Claims
- Application Information
AI Technical Summary
Problems solved by technology
Method used
Image
Examples
Embodiment 1
[0062] Such as figure 2 As shown, the structure of this embodiment is the same as the above-mentioned figure 1 The structure is basically the same, the differences are: the hollow air duct 36 of the middle wall 8 is provided with a baffle to adjust the air intake; the upper periphery of the pre-combustion chamber 1 and the gasification chamber 30, outside the front wall 5 and the mechanical grate 7 The bottom of each other is provided with the air supply channel 29 that is connected to each other by the air intake from the top of the gasification chamber 30 and the air supply from the bottom of the mechanical grate 7, and the rear wall air supply channel 17 is provided in the flue gas deflection channel 161, and the air supply channel 29 or an external air source supplies air to the semi-coke area 6 of the pre-chamber 1 through the rear wall air supply passage 17.
[0063] Its combustion process is:
[0064] The raw coal enters the left pre-combustion chamber 1 and the gasi...
Embodiment 2
[0074] Such as image 3 as shown, image 3 The structure shown is: the mechanical grate 7 in the pre-combustion chamber 1 is a fixed grate, and the lower end of the rear wall 10 is provided with a baffle plate 37 for adjusting the amount of coke, and the rest are the same as in Embodiment 1.
[0075] There is no active grate in the pre-combustion chamber 1, and the failure rate is low, but the pre-combustion chamber does not operate independently, and the lower coke speed is controlled by the main grate 11 and the focusing amount baffle 37; The layer is very thin (30-50mm), and the coking amount baffle is easy to jam coal, so the focusing amount baffle is designed to be controlled by the heavy hammer and manual cooperation; when only the heavy hammer is controlled, the load increases, the grate speed increases, and the amount of coking Increase; the main grate load of the present embodiment is bigger.
Embodiment 3
[0077] Such as Figure 4 as shown, Figure 4 The structure: the air supply channel A communicating with it is set under the mechanical grate 7 of the pre-combustion chamber 1, and the upper part of the gasification chamber 30 is provided with an S-shaped flue gas deflector box 40, and the two outlets of the flue gas deflector box 40 communicate with the gasification chamber 30 and the flue gas baffle channel 161 respectively, and the others are the same figure 2 . The air supply to the pre-combustion chamber 1 is simplified, but the heat dissipation loss of the pre-combustion chamber 1 and the gasification chamber 30 increases, and the temperature of the primary air entering the pre-combustion chamber 1 is low, and the flue gas deflector box 40 is conducive to the mixing of the components of the flue gas , NOx reduction, and a catalyst can also be added in it under special conditions.
PUM
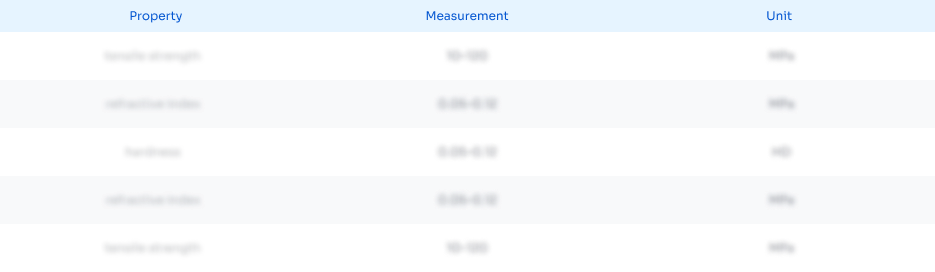
Abstract
Description
Claims
Application Information

- Generate Ideas
- Intellectual Property
- Life Sciences
- Materials
- Tech Scout
- Unparalleled Data Quality
- Higher Quality Content
- 60% Fewer Hallucinations
Browse by: Latest US Patents, China's latest patents, Technical Efficacy Thesaurus, Application Domain, Technology Topic, Popular Technical Reports.
© 2025 PatSnap. All rights reserved.Legal|Privacy policy|Modern Slavery Act Transparency Statement|Sitemap|About US| Contact US: help@patsnap.com