Sintered building brick with high flyash mixing amount and its production process
A technology for fly ash and construction, which is applied in the field of preparation of building bricks by using fly ash and its preparation, which can solve the problems of complex procedures, low proportion of fly ash, long production cycle, etc., and achieves improved drying speed and production The effect of shortening the cycle time and high utilization rate
- Summary
- Abstract
- Description
- Claims
- Application Information
AI Technical Summary
Problems solved by technology
Method used
Image
Examples
Embodiment 1
[0034] The first step: get fly ash, sodium bentonite and the additive that is made up of 80% magnesium sulfide, 15% ferric oxide and 5% ferrous oxide by the weight ratio of 85,12,3, press figure 1 The process shown: first, transport the three to the mixer, mix and stir; the second step, transport the stirred soil material to the wheel mill for grinding, and grind it into a soil material smaller than 0.088mm; the third step The first step is to take 18 parts by weight of water and pour it into the soil material one after another, and then use the mixer for secondary mixing; the fourth step is to send the mixed mud into the brick making machine to make bricks; the fifth step is to make the bricks Put it on the drying car and send it into the drying hole with both ends open in turn, and move forward slowly. The adobe is controlled in about 8 hours from entering the hole to exiting the other hole. Its drying process is as figure 2 As shown, the waste heat released when the wheel...
Embodiment 2
[0036] Extract and mix according to the weight ratio of fly ash, sodium bentonite and additive 90:7:8, and then add 20 weight parts of water in the second stirring; other production processes are basically the same as in Example 1.
Embodiment 3
[0038] Extract and mix by weight of fly ash, sodium bentonite and additive 95:5:10, then add 22 parts by weight of water successively during the second stirring, and other production processes are basically the same as in Example 1.
[0039] In the drying process of Examples 2 and 3, the running time of the bricks in the drying tunnel is adjusted according to the difference in water content of the bricks and the difference in the amount of waste heat extracted. According to experiments, it can be controlled at about 10 and 13 hours respectively under the above conditions. The proportion of magnesium sulfide in the additives in these two embodiments is selected at 85%, and the content of ferric oxide and ferrous oxide is selected at about 7%.
PUM
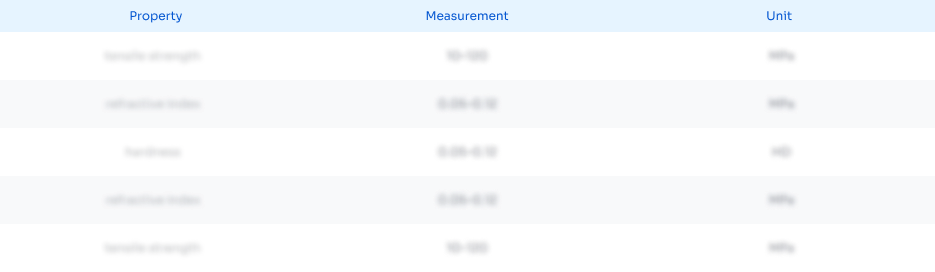
Abstract
Description
Claims
Application Information

- R&D Engineer
- R&D Manager
- IP Professional
- Industry Leading Data Capabilities
- Powerful AI technology
- Patent DNA Extraction
Browse by: Latest US Patents, China's latest patents, Technical Efficacy Thesaurus, Application Domain, Technology Topic, Popular Technical Reports.
© 2024 PatSnap. All rights reserved.Legal|Privacy policy|Modern Slavery Act Transparency Statement|Sitemap|About US| Contact US: help@patsnap.com