Making process of RE luminous fiber
A technology of luminous fiber and manufacturing method, applied in the textile field, can solve the problems that affect the development, utilization and popularization of luminous fiber, cannot fully meet actual needs, and the manufacturing method is unreasonable, etc., and achieve excellent uniformity and stability. , Reduce high temperature and price reduction, and ensure the effect of normal progress
- Summary
- Abstract
- Description
- Claims
- Application Information
AI Technical Summary
Problems solved by technology
Method used
Examples
Embodiment 1
[0014] After drying the tackified polyester chips at a temperature of 100°C for 25 hours, add a luminous agent at a ratio of 30%, and then add 0.03% of a flow stabilizer, 0.04% of an oxidation stabilizer, 0.05% of an anti-ultraviolet agent, and Linking agent 0.04%, carrier 0.3%, and then melted at 250 ° C, injected, pelletized, and made into masterbatch; which is composed of flow stabilizer, oxidation stabilizer, anti-ultraviolet agent, cross-linking agent and carrier The additives are nanoscale;
[0015] Then prepare the above-mentioned masterbatch and large bright silk slices at a ratio of 10%, and after drying at 100°C for 25 hours, in the screw with a melting temperature of 280°C and a winding speed of 3000 m / min Spinning and winding to make POY yarn;
[0016] Then the above POY yarn is processed on a high-speed elastic yarn machine, wherein the temperature of the upper hot box is 190°C, the temperature of the lower hot box is 170°C, the underfold is 1.7, the ratio of the...
Embodiment 2
[0018] After drying the tackified polyester chips at a temperature of 120°C for 15 hours, add a luminous agent in a proportion of 15%, and then add 0.01% of a flow stabilizer, 0.02% of an oxidation stabilizer, 0.01% of an anti-ultraviolet agent, and Linking agent 0.03%, carrier 0.1%, and then melted at 250 ° C, injected, pelletized, and made into masterbatch; which is composed of flow stabilizer, oxidation stabilizer, anti-ultraviolet agent, cross-linking agent and carrier The additives are nanoscale;
[0019] Then prepare the above-mentioned masterbatch and large bright silk slices at a ratio of 6%, and after drying at a temperature of 120°C for 15 hours, in the screw at a melting temperature of 280°C and a winding speed of 3000 m / min Spinning and winding to make POY yarn;
[0020] Then the above POY yarn is processed on a high-speed elastic yarn machine, wherein the temperature of the upper hot box is 170°C, the temperature of the lower hot box is 150°C, the underfold is 1....
Embodiment 3
[0022] After drying the tackified polyester chips at a temperature of 110°C for 20 hours, add a luminous agent at a ratio of 22.5%, and then add 0.02% of a flow stabilizer, 0.03% of an oxidation stabilizer, 0.03% of an anti-ultraviolet agent, and Linking agent 0.035%, carrier 0.2%, and then melted at 251 ° C, injected into tape, pelletized, and made into masterbatch; which is composed of flow stabilizer, oxidation stabilizer, anti-ultraviolet agent, crosslinking agent and carrier The additives are nanoscale;
[0023] Then prepare the above-mentioned masterbatch and large bright silk slices at a ratio of 8%, and after drying at a temperature of 110°C for 20 hours, in the screw at a melting temperature of 290°C and a winding speed of 3100 m / min Spinning and winding to make POY yarn;
[0024] Then the above POY yarn is processed on a high-speed elastic yarn machine, wherein the temperature of the upper hot box is 180°C, the temperature of the lower hot box is 160°C, the underfol...
PUM
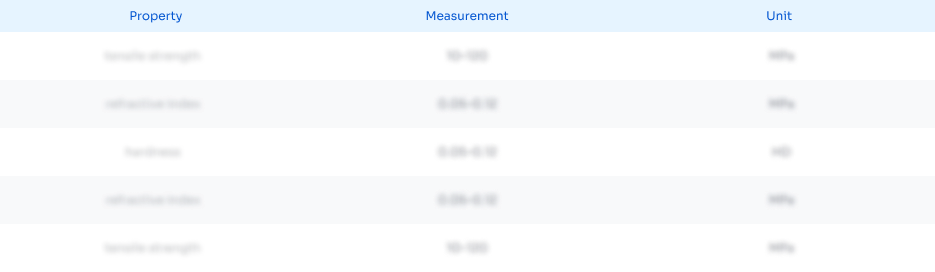
Abstract
Description
Claims
Application Information

- R&D Engineer
- R&D Manager
- IP Professional
- Industry Leading Data Capabilities
- Powerful AI technology
- Patent DNA Extraction
Browse by: Latest US Patents, China's latest patents, Technical Efficacy Thesaurus, Application Domain, Technology Topic, Popular Technical Reports.
© 2024 PatSnap. All rights reserved.Legal|Privacy policy|Modern Slavery Act Transparency Statement|Sitemap|About US| Contact US: help@patsnap.com