Process for preparing deoxidant used in smelting steel and its composite rare-earth deoxidant
A deoxidizer and preparation method technology, applied in the field of olefin deoxidizer, can solve the problems of low equipment productivity, high raw material price, and high smelting temperature, and achieve the effects of low production cost, improved mechanical properties, and low smelting temperature.
- Summary
- Abstract
- Description
- Claims
- Application Information
AI Technical Summary
Problems solved by technology
Method used
Examples
Embodiment 1
[0021] The horizontal reverberatory furnace used is a single-chord horseshoe-shaped regenerative glass melting furnace with a volume of 4000mm×2300mm×1600mm, and the refractory material is magnesia-aluminum bricks. Use heavy oil as fuel. The raw material formula of the rare earth deoxidizer used in the steelmaking process is:
[0022] Iron Ore 40% Bauxite 15%
[0023] Quartz Sand 10% Manganese Ore 8%
[0024] Carbonite 19% Misch 8%
[0025] Add 8% charcoal of the total weight of the above-mentioned ore, pulverize to 90% and pass through a 20-mesh sieve, and mix evenly. Before starting the furnace, add 1000 kg of the above-mentioned prepared raw materials, spray heavy oil and oxygen-enriched air (24% oxygen ), heated until the temperature in the furnace reached 1350°C, and maintained for 30 minutes, then began to discharge, and at the same time continuously added crushed ore raw materials, the feeding speed was 1000 kg / hour, and the discharging speed was about 700 kg / hour. ...
Embodiment 2
[0027] Equipment method is with embodiment 1, and raw material formula is:
[0028] Iron Ore 38% Bauxite 12%
[0029] Quartz Sand 9% Manganese Ore 14%
[0030] Carbonite 18% Misch 9%
[0031] The allotment of charcoal is with embodiment 1.
[0032] Crush the ore until 90% pass through a 20-mesh sieve and mix well. Spray heavy oil and air (containing 21% oxygen) to heat the furnace to a temperature of 1300°C and keep it for 60 minutes, start discharging and simultaneously add crushed ore raw materials continuously, the feeding speed is 1000 kg / h, and the discharging speed is about 700 kg / h At this time, the molten rare earth composite deoxidizer becomes solid after cooling, and its composition is: Fe: 39.4%; Al: 8.7%; Si: 12.8%; Mn: 14.6%; Ca: 17.9%; RE: 6.2%.
Embodiment 3
[0034] Equipment method is with embodiment 1, and raw material formula is:
[0035] Iron Ore 34% Bauxite 8%
[0036] Quartz Sand 12% Manganese Ore 13%
[0037] Carbonite 17% Barite 10% Mixed Rare Earth 6%
[0038] The input amount of charcoal is 13% of the total weight of ore.
[0039] Crush the ore until 90% pass through a 20-mesh sieve and mix well. Spray heavy oil and oxygen-enriched air (28% oxygen) to heat the furnace to a temperature of 1370-1390°C, and keep it for 60 minutes, then start discharging, and simultaneously add crushed ore raw materials continuously at a feeding speed of 1000 kg / hour, and discharge The speed is about 700 kg / h, and the molten rare earth composite deoxidizer becomes solid after cooling, and its composition is: Fe: 35.4%; Al: 6.8%; Si: 14.6%; Mn: 12.8%; Ca: 18.2%; Ba: 7.1%; RE: 5.0%.
PUM
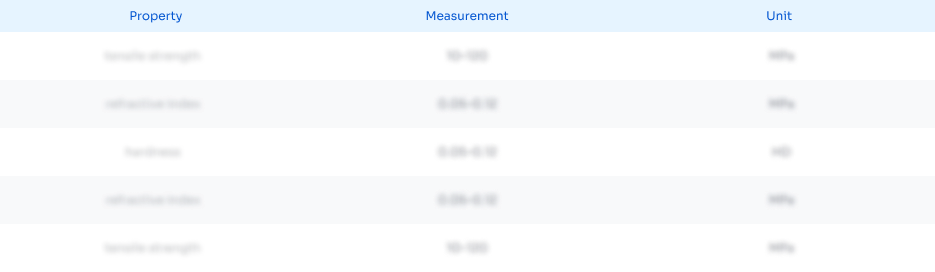
Abstract
Description
Claims
Application Information

- Generate Ideas
- Intellectual Property
- Life Sciences
- Materials
- Tech Scout
- Unparalleled Data Quality
- Higher Quality Content
- 60% Fewer Hallucinations
Browse by: Latest US Patents, China's latest patents, Technical Efficacy Thesaurus, Application Domain, Technology Topic, Popular Technical Reports.
© 2025 PatSnap. All rights reserved.Legal|Privacy policy|Modern Slavery Act Transparency Statement|Sitemap|About US| Contact US: help@patsnap.com