Cooling method of bulk PVC resin polymerization
A technology of polyvinyl chloride resin and cooling method, which is applied in the field of cooling by polymerization stirrer, can solve the problems of no polymerization stirrer providing cooling medium, delay of production cycle, poor heat exchange effect, etc., shorten the polymerization production cycle, reduce Polymerization sticky kettle, the effect of high-grade product rate improvement
- Summary
- Abstract
- Description
- Claims
- Application Information
AI Technical Summary
Problems solved by technology
Method used
Examples
Embodiment
[0012] Embodiment: produce polyvinyl chloride according to the method of comparative example, the cooling medium in the polymerization stirrer is changed into respectively 5 ℃, 10 ℃ and 15 ℃ circulating chilled water, in polyvinyl chloride polymerization reaction process, this circulating chilled water The medium in the polymerization tank is cooled by the polymerization stirrer, so that the medium in the polymerization tank is kept within the normal temperature range required by the polyvinyl chloride polymerization reaction, and the circulating chilled water after heat exchange flows out of the polymerization stirrer, and then passes through the cooler Cool down to 5°C, 10°C and 15°C respectively, and pass into the polymerization stirrer again for recycling.
[0013] The average period of each batch of material produced by this method is 7.6 hours, and the output of each batch of material is 18 tons. The annual calculation is 8,000 hours. The price of polyvinyl chloride resin...
PUM
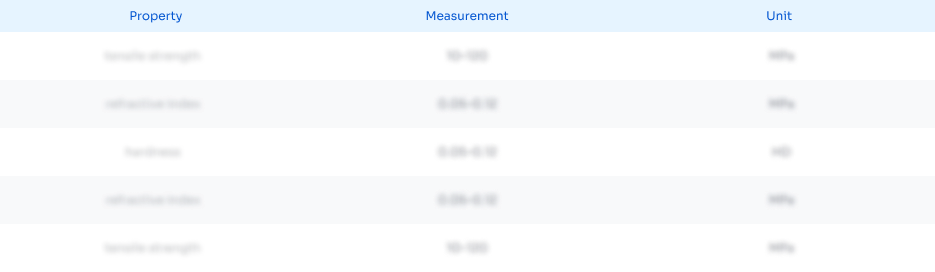
Abstract
Description
Claims
Application Information

- R&D Engineer
- R&D Manager
- IP Professional
- Industry Leading Data Capabilities
- Powerful AI technology
- Patent DNA Extraction
Browse by: Latest US Patents, China's latest patents, Technical Efficacy Thesaurus, Application Domain, Technology Topic, Popular Technical Reports.
© 2024 PatSnap. All rights reserved.Legal|Privacy policy|Modern Slavery Act Transparency Statement|Sitemap|About US| Contact US: help@patsnap.com