Furnace roller thermal insulation protection process
A technology of heat insulation protection and furnace roll, applied in the direction of furnace grate, roll, manufacturing tools, etc., can solve the problems of easy cracking and peeling damage, affecting production efficiency, and consuming labor hours, etc. , The effect of simple and convenient process
- Summary
- Abstract
- Description
- Claims
- Application Information
AI Technical Summary
Problems solved by technology
Method used
Examples
Embodiment Construction
[0006] Specific embodiments of the present invention are described in detail below.
[0007] The specific process of the present invention is as follows: Step 1: brush the special high-temperature adhesive for the furnace roller on the designated heat insulation part of the furnace roller of the load-bearing product wheel. When painting, the surface of the furnace roller must not have oil stains, and the surface finish is not lower than 4; The second step: place the specially shaped ceramic fiber block on the above-mentioned part, and brush the high-temperature adhesive on the interface, and then pressurize and fix it initially; the third step: keep the surface of the ceramic fiber block clean, and then spray the furnace on the surface High-temperature infrared compound liquid emulsion specially used for rollers, dry in the shade for later use; Step 4: place heat-resistant steel fastening buckles on the ceramic fiber block sprayed with high-temperature infrared compound emuls...
PUM
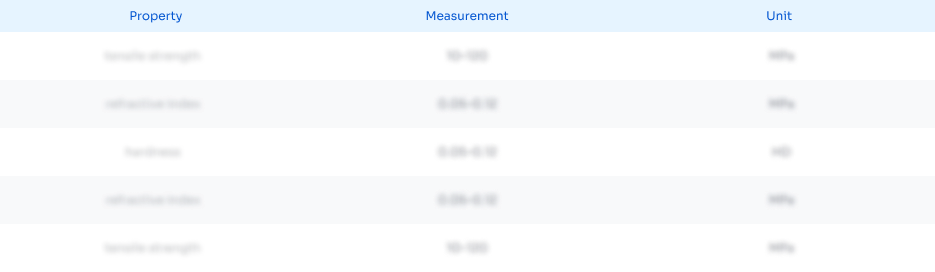
Abstract
Description
Claims
Application Information

- Generate Ideas
- Intellectual Property
- Life Sciences
- Materials
- Tech Scout
- Unparalleled Data Quality
- Higher Quality Content
- 60% Fewer Hallucinations
Browse by: Latest US Patents, China's latest patents, Technical Efficacy Thesaurus, Application Domain, Technology Topic, Popular Technical Reports.
© 2025 PatSnap. All rights reserved.Legal|Privacy policy|Modern Slavery Act Transparency Statement|Sitemap|About US| Contact US: help@patsnap.com