Hard polyvinyl-chloride plastic plate and producing recipe
A technology for rigid polyvinyl chloride and plastic sheets, which is applied in the field of formulation of rigid polyvinyl chloride plastic sheets, and can solve problems such as thermal insulation, fire prevention, sound insulation, poor secondary processing performance, fire protection grades that do not meet the requirements for use, and high manufacturing costs. , to achieve the effects of outstanding fire performance, reduced raw material costs, and simple manufacturing process
- Summary
- Abstract
- Description
- Claims
- Application Information
AI Technical Summary
Problems solved by technology
Method used
Examples
Embodiment 1
[0027] 16% of polyvinyl chloride resin, 25% of aggregate powder (composed of talcum powder, magnesium powder, aluminum powder and kaolin powder), 15% of porosity agent (composed of calcite powder, aluminum oxide powder and baking soda powder ), 4% of organic foaming agent (composed of N, N'-dinitropentamethylenetetramine (commonly known as DPT), azodicarbonamide and azobisisobutyronitrile), respectively added to the mixer Stir to make it evenly mixed; then add 40% toluene to the mixture until it becomes a uniform fluid. Pour the mixed raw materials into the mold of the hydraulic press, and set the heating time and temperature according to the structure of the press and mold and the capacity of the inner cavity. The pressure value of the press is set at 18Mpa, the heating time is 55-65 minutes, and the temperature is 160-180°C. After the heating is completed, cool down until the mold is cold, then release the pressure and discharge the material. Then the molded material is se...
Embodiment 2
[0029] 20% of polyvinyl chloride resin, 23% of aggregate powder (composed of talcum powder, magnesium powder, aluminum powder and kaolin powder), 13% of porosity agent (composed of calcite powder, aluminum oxide powder and baking soda powder ), 6% of organic blowing agent [composed of N, N'-dinitropentamethylenetetramine (commonly known as DPT), azodicarbonamide and azobisisobutyronitrile], respectively added to the mixer Stir to make it evenly mixed; then add 38% toluene to the mixture until it becomes a uniform fluid. Pour the mixed raw materials into the mold of the hydraulic press, and set the heating time and temperature according to the structure of the press and mold and the capacity of the inner cavity. The pressure value of the press is set at 18Mpa, the heating time is 55-65 minutes, and the temperature is 160-180°C. After the heating is completed, cool down until the mold is cold, then release the pressure and discharge the material. Then the molded material is se...
Embodiment 3
[0031] 24% of polyvinyl chloride resin, 20% of aggregate powder (composed of talcum powder, magnesium powder, aluminum powder and kaolin powder), 12% of porosity agent (composed of calcite powder, aluminum oxide powder and baking soda powder ), 7% of organic foaming agent [composed of N, N'-dinitropentamethylenetetramine (commonly known as DPT), azodicarbonamide and azobisisobutyronitrile], respectively added to the mixer Stir to make it evenly mixed; then add 37% toluene to the mixture until it becomes a uniform fluid. Pour the mixed raw materials into the mold of the hydraulic press, and set the heating time and temperature according to the structure of the press and mold and the capacity of the inner cavity. The pressure value of the press is set at 18Mpa, the heating time is 55-65 minutes, and the temperature is 160-180°C. After the heating is completed, cool down until the mold is cold, then release the pressure and discharge the material. Then the molded material is se...
PUM
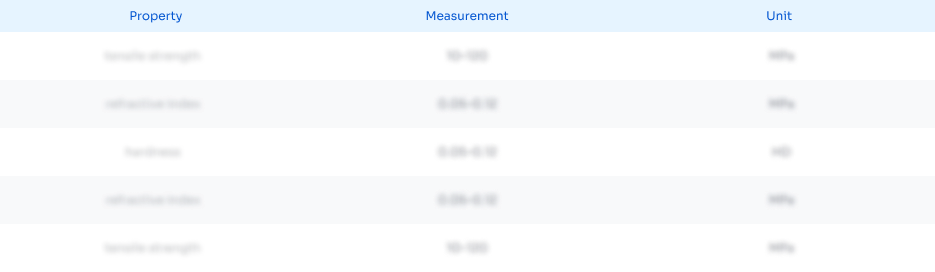
Abstract
Description
Claims
Application Information

- Generate Ideas
- Intellectual Property
- Life Sciences
- Materials
- Tech Scout
- Unparalleled Data Quality
- Higher Quality Content
- 60% Fewer Hallucinations
Browse by: Latest US Patents, China's latest patents, Technical Efficacy Thesaurus, Application Domain, Technology Topic, Popular Technical Reports.
© 2025 PatSnap. All rights reserved.Legal|Privacy policy|Modern Slavery Act Transparency Statement|Sitemap|About US| Contact US: help@patsnap.com