Method for selectively electroplating strip-shaped metal support material
A local electroplating and strip-shaped technology, applied in the direction of electrophoretic plating, electrolysis, electrolytic coating, etc., can solve the problems of expensive paint materials, extremely difficult accumulation of paint, damage to the substrate, etc., to achieve rapid removal, increased travel speed, and prevent base The effect of material damage
- Summary
- Abstract
- Description
- Claims
- Application Information
AI Technical Summary
Problems solved by technology
Method used
Image
Examples
Embodiment Construction
[0031] figure 1 The illustrated electroplating plant for partial plating of base strips is designed as a so-called reel-to-roll plant, in which the metal base strip 10 is continuously unwound from a first drum or reel 11 and passes through the electroplating plant again as a finished processed strip The material is rolled onto a second drum or reel 12. In this case, belt speeds of 20 m / min or higher are feasible.
[0032] First, the base tape 10 passes through a preparation station 13 where the base tape 10 is cleaned, activated and rinsed.
[0033] Next, the base strip 10 passes through a painting station 14, where partial electrophoretic painting is carried out. The painting station 14 may include one or more painting units 15, such as figure 2 as indicated. Such a painting unit generally comprises an encapsulating housing which is protected against uncontrolled deposition of paint in unintended areas. For this purpose, the webs 17 , 18 , which are made of Teflon or an...
PUM
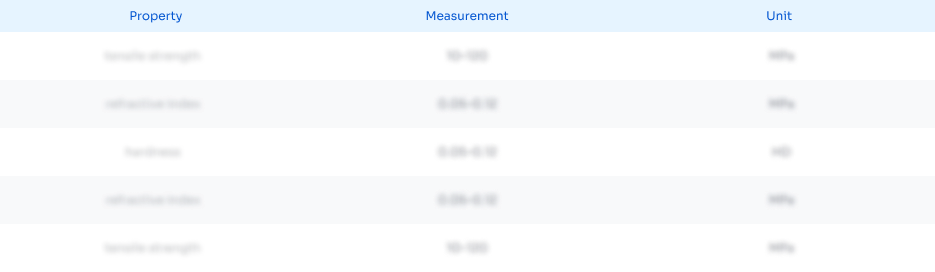
Abstract
Description
Claims
Application Information

- R&D
- Intellectual Property
- Life Sciences
- Materials
- Tech Scout
- Unparalleled Data Quality
- Higher Quality Content
- 60% Fewer Hallucinations
Browse by: Latest US Patents, China's latest patents, Technical Efficacy Thesaurus, Application Domain, Technology Topic, Popular Technical Reports.
© 2025 PatSnap. All rights reserved.Legal|Privacy policy|Modern Slavery Act Transparency Statement|Sitemap|About US| Contact US: help@patsnap.com