Wetting dry pot dynamic composite rectifying process of thermosensitive material
A rectification process and material technology, which is applied in the direction of distillation and fractionation in the boiler/distillate, to achieve the effects of short rectification time, high yield and low thermal decomposition rate of materials
- Summary
- Abstract
- Description
- Claims
- Application Information
AI Technical Summary
Problems solved by technology
Method used
Image
Examples
Embodiment 1
[0017] Embodiment 1: The raw material is 60% (mass percentage) of heat-sensitive material 4-hydroxy-2-butanone, which contains 14% (mass percentage) of light impurities and 26% (mass percentage) of heavy impurities. Add heat carrier white oil into the wet dry kettle, turn on the circulating pump, heat exchanger, and condenser, and use 50L / h from the feed port in the tower to the diameter of φ300 packing layer with a height of 8 meters (the packing is divided into two sections, each Section 4 meters) rectifying tower feed, then rectifying tower starts to run, carries out total reflux operation 0.5 hour earlier, then by mining heavy impurity at the bottom of the tower, the discharge rate is 14L / h, and the reflux flow at the top of the tower is 10L / h h, the remaining liquid at the top of the tower accumulates in the reflux tank. After the feed in the tower is completed, reduce the discharge rate at the bottom of the tower to 8L / h, and increase the return flow at the top of the to...
PUM
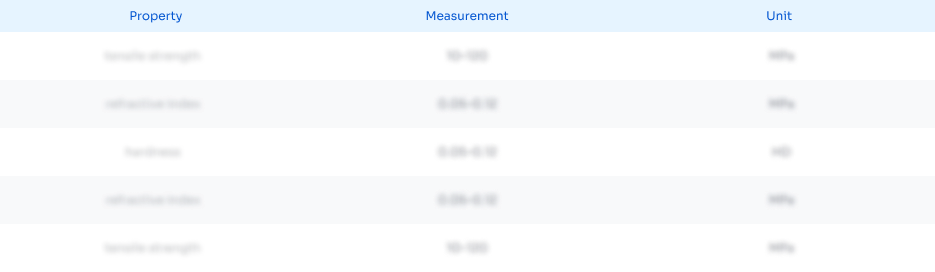
Abstract
Description
Claims
Application Information

- Generate Ideas
- Intellectual Property
- Life Sciences
- Materials
- Tech Scout
- Unparalleled Data Quality
- Higher Quality Content
- 60% Fewer Hallucinations
Browse by: Latest US Patents, China's latest patents, Technical Efficacy Thesaurus, Application Domain, Technology Topic, Popular Technical Reports.
© 2025 PatSnap. All rights reserved.Legal|Privacy policy|Modern Slavery Act Transparency Statement|Sitemap|About US| Contact US: help@patsnap.com