Preparation process of dye-resistant powder paste
A preparation process and technology of anti-dye powder, applied in the direction of climate sustainability, filling slurry, sustainable waste treatment, etc., can solve the problems of easy cracking of putty, strong alkalinity, low adhesion, etc. Good, smooth wall, good water resistance
- Summary
- Abstract
- Description
- Claims
- Application Information
AI Technical Summary
Problems solved by technology
Method used
Examples
Embodiment 1
[0025] A preparation process of an anti-dye powder paste comprises: materials and processes;
[0026] The materials include the following:
[0027] S1. Raw materials: cementitious materials, fillers, additives, auxiliary materials and water; activated calcium carbonate, bentonite, polyvinyl alcohol, cellulose ether, sodium hexametaphosphate and water;
[0028] S2. The proportion of the cementitious material is 5%, the proportion of the filler is 95%, the proportion of the auxiliary agent is 9.3%, and the proportion of the auxiliary material is 2.2% %, and the proportion of the water is 55%.
[0029] The cementitious material is an emulsion, and the emulsion has many characteristics such as high bonding strength, water resistance and environmental protection.
[0030] The fillers are heavy calcium carbonate, light calcium carbonate and talc, the content of the heavy calcium carbonate is 65%, the content of the light calcium carbonate is 10%, and the talc is The proportion of...
Embodiment 2
[0043] A preparation process of anti-dye powder paste comprises the following steps:
[0044] The first step: select the emulsion as the cementitious material, and the amount of the cementitious material is 10%, and then add the filler to mix and stir evenly, and the time is 5-10min;
[0045] The second step: the auxiliary agent is added to the first step, and then mixed and stirred for 10 to 15 minutes;
[0046] The third step: add the auxiliary materials into the second step, and then mix and stir until there is no agglomeration, resulting in putty powder;
[0047] Step 4: Mix and stir the putty powder and water until the putty powder becomes a powder paste.
[0048] The type and amount of cementitious material have the most obvious influence on the bonding strength and water resistance of putty. The bonding strength of putty increases with the increase of the amount of cementitious material. However, if the amount is too large, it will affect the sandability, and it is not...
Embodiment 3
[0050] A preparation process of anti-dye powder paste comprises the following steps:
[0051] The first step: select the emulsion as the cementitious material, and then add the filler to mix and stir evenly, the time is 5-10min;
[0052] The second step: adding the auxiliary agent into the first step, and then mixing and stirring for 10 to 15 minutes, and the proportion of suspending agent-bentonite in the auxiliary agent is 0.7%;
[0053] The third step: add the auxiliary materials into the second step, and then mix and stir until there is no agglomeration, resulting in putty powder;
[0054] Step 4: Mix and stir the putty powder and water until the putty powder becomes a powder paste.
[0055] According to the content of different anti-settling agents to observe the state of the putty, it is found that when the content is low, delamination is easy to occur in a short time, and when the content is too large, although there is no delamination, the cost is too high, which affe...
PUM
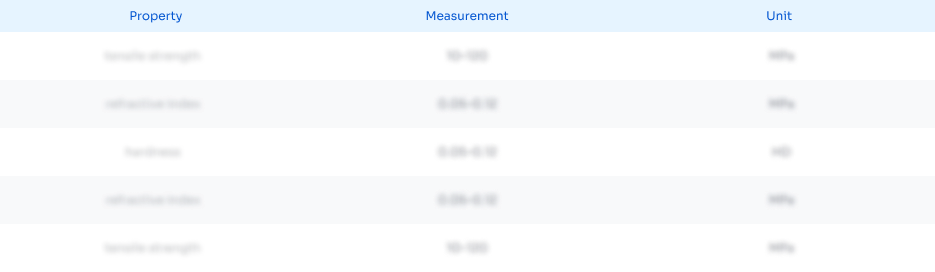
Abstract
Description
Claims
Application Information

- R&D Engineer
- R&D Manager
- IP Professional
- Industry Leading Data Capabilities
- Powerful AI technology
- Patent DNA Extraction
Browse by: Latest US Patents, China's latest patents, Technical Efficacy Thesaurus, Application Domain, Technology Topic, Popular Technical Reports.
© 2024 PatSnap. All rights reserved.Legal|Privacy policy|Modern Slavery Act Transparency Statement|Sitemap|About US| Contact US: help@patsnap.com