Multi-way valve body inner cavity mud core, manufacturing method of multi-way valve body inner cavity mud core and runner core manufactured by multi-way valve body inner cavity mud core
A multi-way valve and core technology, which is applied in the field of foundry sand cores, can solve the problems of low economic cost, high core cost, and low core strength, and achieve the effects of low economic cost, low cost, and reduced core-making costs
- Summary
- Abstract
- Description
- Claims
- Application Information
AI Technical Summary
Problems solved by technology
Method used
Image
Examples
Embodiment 1
[0032] A multi-way valve valve body cavity core of this embodiment includes a core body, and the core body is formed by mixing ceramsite sand and coated sand. The mixed sand is formed by a hot coating method core shooting machine. The surface of the core body is sequentially brushed with an anti-adhesion film layer and a high-strength refractory coating. The molding sand formed by the mixing of ceramsite sand and coated sand has good strength and solidification molding performance. Compared with the core-making scheme of pearl sand, the core made of the above-mentioned mixed sand has higher strength, and the cost is very good. control. The anti-adhesion film layer can quickly form a film on the surface of the core, which can prevent the coating from immersing into the core and reduce the strength of the core. The high-strength refractory coating has high strength, fire resistance and excellent dip coating performance, which further improves the core. strength and fire resista...
Embodiment 2
[0036] This embodiment discloses a method for manufacturing a valve body cavity core of a multi-way valve, which is used for manufacturing the valve body cavity core of the multi-way valve in Embodiment 1 above. combine figure 1 As shown, the method includes the following steps:
[0037]S1. Forming sand preparation: mix ceramsite sand and coated sand in proportion to form mixed sand. Preferably, the weight ratio of the ceramsite sand and the coated sand is 3:1, which takes into account the cost of the mixed sand and the curing and molding performance, and greatly improves the strength and fire resistance of the core.
[0038] S2. Ni core forming: The mixed mixed sand is shaped by a hot film core shooting machine to make a Ni core body. The molding process of the core-shooting machine by the thermal lamination method is the prior art, which will not be described further.
[0039] S3. Dip coating of the core: The body of the core has undergone two dip-coating treatments. The ...
Embodiment 3
[0042] This embodiment discloses a multi-way valve body cavity flow channel core, which is assembled and assembled by at least two cores, and the core is manufactured by the manufacturing method of the multi-way valve body cavity core of the above-mentioned embodiment 2 made. Using the above-mentioned Ni core to make the flow channel core in the valve body cavity of the multi-way valve can effectively improve the strength of the flow channel core and improve the qualification rate of the product under the condition of reducing the cost of core making.
[0043] The flow channel core is assembled by several pieces of Ni cores, which depends on the structure of the valve body cavity of the multi-way valve. Different from the existing runner core structure, in this embodiment, the upper and lower adjacent cores are matched by a positioning and top structure, that is, an upwardly extending plug is provided on the core located at the lower part. There is a positioning groove matche...
PUM
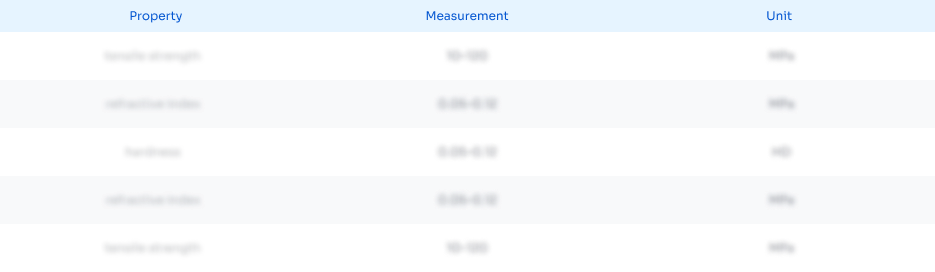
Abstract
Description
Claims
Application Information

- Generate Ideas
- Intellectual Property
- Life Sciences
- Materials
- Tech Scout
- Unparalleled Data Quality
- Higher Quality Content
- 60% Fewer Hallucinations
Browse by: Latest US Patents, China's latest patents, Technical Efficacy Thesaurus, Application Domain, Technology Topic, Popular Technical Reports.
© 2025 PatSnap. All rights reserved.Legal|Privacy policy|Modern Slavery Act Transparency Statement|Sitemap|About US| Contact US: help@patsnap.com