Cleaning system and method for ultrafiltration membrane
A cleaning system and ultrafiltration membrane technology, applied in ultrafiltration, chemical instruments and methods, membrane technology, etc., can solve the problems of reducing the water production time of membrane system, decline in filtration performance, membrane corrosion, etc., to reduce backwashing and chemical The effect of cleaning frequency, reducing the content of organic matter in the effluent, and improving the overall online rate
- Summary
- Abstract
- Description
- Claims
- Application Information
AI Technical Summary
Problems solved by technology
Method used
Image
Examples
Embodiment 1
[0051] This embodiment provides a cleaning system for an ultrafiltration membrane, such as figure 1 As shown, the system includes a raw water tank 1, an ultrafiltration inlet pump 2, a self-cleaning filter 3, an ultrafiltration device 5, a water production tank 6, an exhaust gas destruction device 14, a backwash water pump 7, an air compressor subsystem 12, and an ozone generator. Subsystem and dosing and cleaning subsystem;
[0052] The ozone generator subsystem includes a mixer 4 and an ozone generator 13;
[0053] The water outlet of the raw water tank 1, the ultrafiltration water inlet pump 2, the mixer 4, the self-cleaning filter 3, the ultrafiltration equipment 5 and the water inlet of the water production tank 6 are connected in sequence; The top of the water tank 6 is used to recover the ozone entering the water production tank 6;
[0054] The ozone generator 13 communicates with the mixer 4;
[0055] The top product water outlet 19 of the ultrafiltration device 5 i...
Embodiment 2
[0060] This embodiment provides a cleaning system for an ultrafiltration membrane, such as figure 2 As shown, the system includes a raw water tank 1, an ultrafiltration inlet pump 2, a self-cleaning filter 3, an ultrafiltration device 5, a water production tank 6, an exhaust gas destruction device 14, a backwash water pump 7, an air compressor subsystem 12, and an ozone generator. Subsystem and dosing and cleaning subsystem;
[0061] The water outlet of the raw water tank 1, the ultrafiltration water inlet pump 2, the self-cleaning filter 3, the ultrafiltration equipment 5 and the water inlet of the water production tank 6 are connected in turn; the exhaust gas destruction device 14 is arranged on the top of the water production tank 6 , for recovering the ozone entering into the water production tank 6;
[0062] The top product water outlet 19 of the ultrafiltration device 5 is also communicated with the product water outlet of the water product tank 6 through the backwash ...
Embodiment 3
[0068] The present embodiment provides a cleaning method for an ultrafiltration membrane. The method adopts the system described in Embodiment 1 and includes the following steps:
[0069] S1: When the liquid level meter detects that the liquid level in the raw water tank 1 reaches the starting liquid level, the ultrafiltration feed pump 2 is automatically turned on, and the raw water in the raw water tank 1 and the ozone from the ozone generator 13 are transported to the The mixer 4 and the self-cleaning filter 3 preliminarily filter out the impurities of larger particles in the water, and through the self-cleaning filter 3 and the mixer 4, the ozone is fully contacted with the organic pollutants in the raw water, and an oxidation reaction occurs. , to completely decompose organic pollutants;
[0070] The dosage of the ozone is 10 mg / L;
[0071] S2: After the raw water that has undergone the oxidative decomposition is sent to the ultrafiltration equipment 5 for filtration, it...
PUM
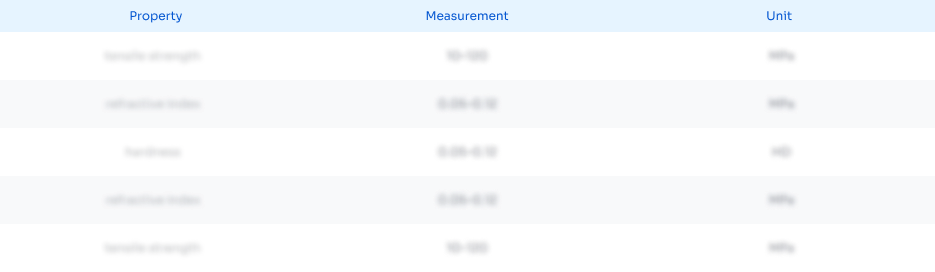
Abstract
Description
Claims
Application Information

- R&D
- Intellectual Property
- Life Sciences
- Materials
- Tech Scout
- Unparalleled Data Quality
- Higher Quality Content
- 60% Fewer Hallucinations
Browse by: Latest US Patents, China's latest patents, Technical Efficacy Thesaurus, Application Domain, Technology Topic, Popular Technical Reports.
© 2025 PatSnap. All rights reserved.Legal|Privacy policy|Modern Slavery Act Transparency Statement|Sitemap|About US| Contact US: help@patsnap.com