Double-sided etching device and etching process for metal radiating fin
A double-sided etching and heat sink technology, applied in the field of etching, can solve problems such as low efficiency, repeated positioning errors, and increased production costs
- Summary
- Abstract
- Description
- Claims
- Application Information
AI Technical Summary
Problems solved by technology
Method used
Image
Examples
Embodiment Construction
[0037] In order to facilitate the understanding of those skilled in the art, the present invention will be further described below with reference to the embodiments and the accompanying drawings, and the contents mentioned in the embodiments are not intended to limit the present invention. The present invention will be described in detail below with reference to the accompanying drawings.
[0038] like Figure 1 to Figure 7 As shown in the figure, the present invention provides a double-sided etching device for a metal heat sink, including a spray mechanism (not shown in the figure) and a flip mechanism, the spray mechanism is used to spray the etching solution on the metal heat sink, and the flip mechanism includes a body 1. The first clamping mechanism 2, the first overturning mechanism 3, the second clamping mechanism 4 and the second overturning mechanism 5 are all arranged on the body 1. The first clamping mechanism 2 and the second clamping mechanism 4 are respectively ...
PUM
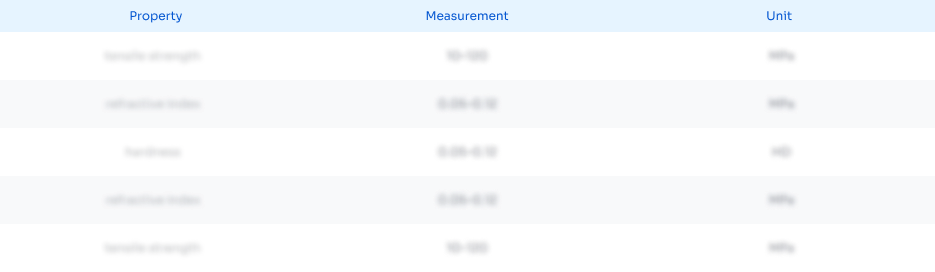
Abstract
Description
Claims
Application Information

- Generate Ideas
- Intellectual Property
- Life Sciences
- Materials
- Tech Scout
- Unparalleled Data Quality
- Higher Quality Content
- 60% Fewer Hallucinations
Browse by: Latest US Patents, China's latest patents, Technical Efficacy Thesaurus, Application Domain, Technology Topic, Popular Technical Reports.
© 2025 PatSnap. All rights reserved.Legal|Privacy policy|Modern Slavery Act Transparency Statement|Sitemap|About US| Contact US: help@patsnap.com