A plasma etching device for etching optical devices
A technology of plasma and optical devices, which is applied in the direction of electrical components, circuits, discharge tubes, etc., can solve the problems of reducing etching efficiency, reducing production efficiency, thick optical devices, etc., and achieves improved etching quality, improved etching efficiency, and groove depth consistent effect
- Summary
- Abstract
- Description
- Claims
- Application Information
AI Technical Summary
Problems solved by technology
Method used
Image
Examples
Embodiment 1
[0028] Embodiment one: if Figure 2-5 As shown, a plasma etching device for etching optical devices, it includes a casing 1, a workbench 2 and a chassis 3 arranged in sequence from top to bottom, the right end of the top of the casing 1 is provided with a gap, and the gap is provided with Airtight cover 4, airtight cover 4 is fixed between shell 1 and cover plate 5 through screw 25, and the top of described shell 1 is provided with cover plate 5, forms between shell 1, cover plate 5, airtight cover 4 and workbench 2 There is a closed cavity 6, and a hollow shaft 7 is installed in the workbench 2 through bearing rotation. The hollow shaft 7 is a plastic part. 8 is provided with a cavity 9, the cavity 9 communicates with the hollow shaft 7, a plurality of suction holes 10 are opened on the top surface of the suction cup 8 and on its edge, and the lower end of the hollow shaft 7 extends downwards in the cabinet 3, The cabinet 3 is provided with a vacuum pump 11 and a motor 12, t...
Embodiment 2
[0041] Embodiment two: if Figure 6~7 As shown, a plasma etching device for etching optical devices. The difference between this embodiment and Embodiment 1 is that an annular tube 33 is arranged in the sealed cavity 6, and the annular tube 33 is located outside the suction cup 8. The annular tube There are a plurality of small holes 34 on the inner ring of 33, and the small holes 34 communicate with the annular pipe 33, and the outer ring of the annular pipe 33 is welded with a branch pipe 35 communicating with the annular pipe 33. The branch pipe 35 runs through the shell 1 and extends to Outside the casing 1 , an air compressor 36 is connected to the extension end of the branch pipe 35 . A bracket 37 is welded to the bottom of the annular pipe 33 , and the bracket 37 is supported on the top surface of the workbench 2 .
[0042] The difference between the work process of this embodiment and embodiment one is:
[0043] After step S6 ends, the operator can turn on the air co...
PUM
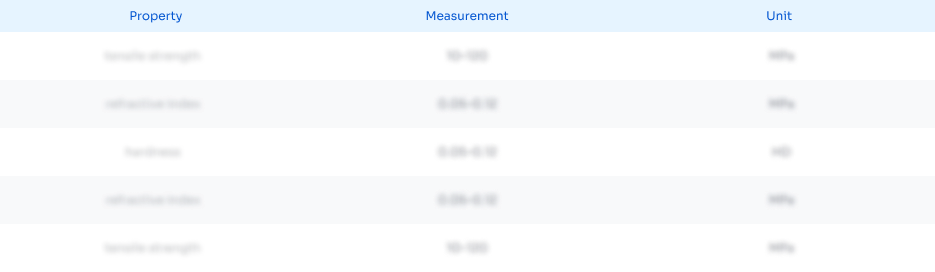
Abstract
Description
Claims
Application Information

- Generate Ideas
- Intellectual Property
- Life Sciences
- Materials
- Tech Scout
- Unparalleled Data Quality
- Higher Quality Content
- 60% Fewer Hallucinations
Browse by: Latest US Patents, China's latest patents, Technical Efficacy Thesaurus, Application Domain, Technology Topic, Popular Technical Reports.
© 2025 PatSnap. All rights reserved.Legal|Privacy policy|Modern Slavery Act Transparency Statement|Sitemap|About US| Contact US: help@patsnap.com