Robot assembly motion planning method based on demonstration trajectory
A technology of motion planning and robotics, applied in the direction of manipulators, program-controlled manipulators, manufacturing tools, etc., to achieve the effects of energy-saving assembly motion planning, solving strange phenomena, and reducing difficulty
- Summary
- Abstract
- Description
- Claims
- Application Information
AI Technical Summary
Problems solved by technology
Method used
Image
Examples
Embodiment Construction
[0048] The technical solutions in the embodiments of the present invention will be clearly and completely described below with reference to the accompanying drawings of the present invention.
[0049] like figure 1 Shown is a schematic diagram of a motion planning system for the installation of electronic components. The system mainly includes actual assembly scene, multimodal sensor module and software algorithm module. The system provides functions such as data acquisition, data transmission, and assembly interaction for the method of the present invention, which is beneficial to the efficient execution of the method.
[0050] Among them, the actual assembly scene includes: PCB board, to-be-plugged-in, robot, workbench and human; the multi-modal sensor module includes: vision sensor, force-torque sensor, robot body sensor; the software module includes: demonstration learning module, Representation learning module and reinforcement learning module.
[0051] like figure 2...
PUM
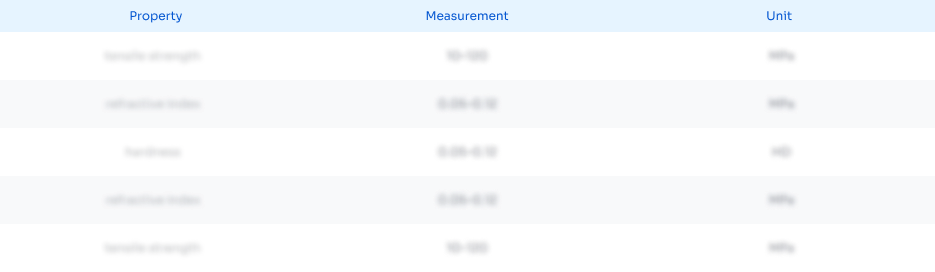
Abstract
Description
Claims
Application Information

- R&D
- Intellectual Property
- Life Sciences
- Materials
- Tech Scout
- Unparalleled Data Quality
- Higher Quality Content
- 60% Fewer Hallucinations
Browse by: Latest US Patents, China's latest patents, Technical Efficacy Thesaurus, Application Domain, Technology Topic, Popular Technical Reports.
© 2025 PatSnap. All rights reserved.Legal|Privacy policy|Modern Slavery Act Transparency Statement|Sitemap|About US| Contact US: help@patsnap.com