Embedded visual tracking control system of autonomous mobile welding robot
A welding robot and autonomous mobile technology, applied in welding equipment, auxiliary welding equipment, program-controlled manipulators, etc., can solve the problems of limited space of welding robots, interference of welding seam tracking accuracy, etc., achieving good real-time performance, clear and stable brightness, Achieving the effect of miniaturization
- Summary
- Abstract
- Description
- Claims
- Application Information
AI Technical Summary
Problems solved by technology
Method used
Image
Examples
Embodiment 1
[0069] like figure 1 As shown, the embedded vision tracking control system for an autonomous mobile welding robot provided by the embodiment of the present invention includes:
[0070] The laser 1 is used to generate structured light and project it onto the surface of the weldment, and the structured light generates an image of distorted stripes at the weld of the weldment 4;
[0071] The industrial camera 2 is used to collect the image of the welding seam including the distortion stripes, the image of the welding gun position and the image of the inclination angle of the welding surface of the weldment 4, and transmit the module to the embedded image processing controller 3 through the 5G network;
[0072] The embedded image processing controller 3 is used to process the welding seam image of the distortion stripe to realize the welding seam tracking; according to the deviation of the welding torch position image and the recognition of the inclination image of the welding sur...
Embodiment 2
[0076] On the basis of Embodiment 1, the laser 1 provided in the embodiment of the present invention is used to generate structured light and project it onto the surface of the weldment, the grating is used to divide the structured light into multi-line structured light, and the industrial camera 2 is used to collect Image of the weld with only multi-line structured light illumination; the grating is placed perpendicular to the optical axis of the laser 1 .
[0077]During the raster scanning process of the primary stable multi-line structure generated by the laser 1, the ARM module is connected to the laser 1, and the photodetector and the micro-galvanometer feedback module are used to calculate the time point at which the position of the micro-galvanometer based on the photodetector is obtained; The FPGA module is connected to the laser 1, uses the pre-stored brightness time correspondence table to match the laser brightness value corresponding to the time point, and uses the ...
Embodiment 3
[0080] On the basis of Embodiment 1, the 5G network transmission module provided by the embodiment of the present invention specifically includes:
[0081] The industrial camera 2 activates the 5G network transmission module, and the industrial camera determines whether it is successfully connected to the 5G network. The 5G network transmission module has a dual-card mode and is compatible with multiple frequency bandwidths BAND, and supports 5G networks of China Telecom, China Mobile, and China Unicom at the same time;
[0082] The industrial camera 2 uploads the welding seam image containing the distortion stripes, the welding torch position image and the inclination image of the welding surface to be welded to the embedded image processing controller 3 through the 5G network transmission module, and turns off the 5G network transmission module.
[0083] The invention transmits the image collected by the industrial camera through the 5G network transmission module, improves ...
PUM
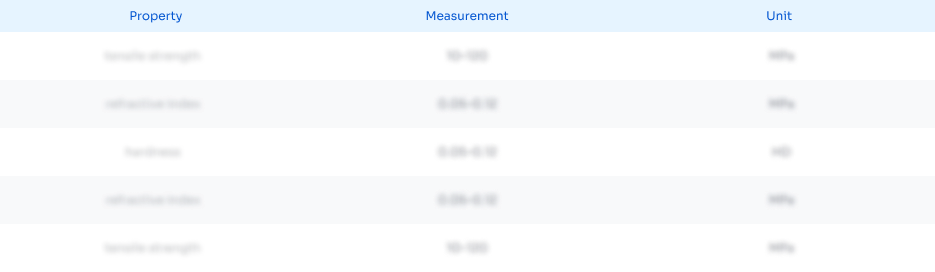
Abstract
Description
Claims
Application Information

- Generate Ideas
- Intellectual Property
- Life Sciences
- Materials
- Tech Scout
- Unparalleled Data Quality
- Higher Quality Content
- 60% Fewer Hallucinations
Browse by: Latest US Patents, China's latest patents, Technical Efficacy Thesaurus, Application Domain, Technology Topic, Popular Technical Reports.
© 2025 PatSnap. All rights reserved.Legal|Privacy policy|Modern Slavery Act Transparency Statement|Sitemap|About US| Contact US: help@patsnap.com