High-precision adjustment method for large-aperture optical lens group
A technology of optical lens and assembly method, which is applied in the field of telescope structure, can solve problems such as increased difficulty in optical lens assembly, decreased surface shape accuracy, and coaxial error, and achieves high application value and innovative effects
- Summary
- Abstract
- Description
- Claims
- Application Information
AI Technical Summary
Problems solved by technology
Method used
Image
Examples
Embodiment 1
[0058] The method of the present invention is proposed based on the discrete multi-point flexible support structure for large-diameter optical lenses. The discrete multi-point flexible support structure for large-diameter optical lenses is such as figure 2 As shown, several indium steel pads 203 are uniformly bonded around the lens, each indium steel pad 203 is provided with a plurality of threaded holes, and is connected between the indium steel pad 203 and the mirror base 201 through a plurality of discrete flexible support units 204 , realizes the connection between the lens 202 and the lens holder 201 and forms an independent lens assembly, and each flexible support unit 204 has multiple directions of flexibility to adapt to the influence of structural deformation or thermal deformation on the mirror surface shape accuracy. The support structure described here does not refer to a specific lens, but a general structural form.
[0059] After each lens and the mirror group f...
PUM
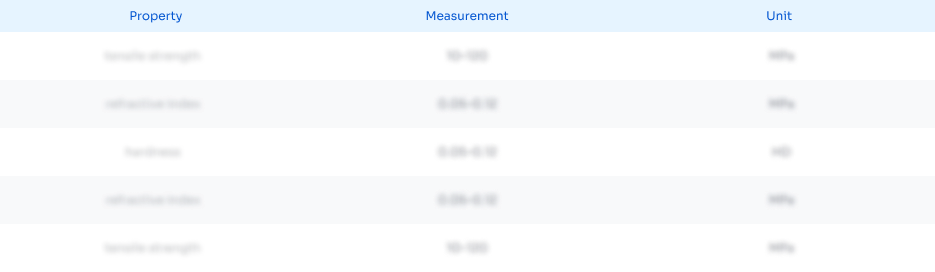
Abstract
Description
Claims
Application Information

- Generate Ideas
- Intellectual Property
- Life Sciences
- Materials
- Tech Scout
- Unparalleled Data Quality
- Higher Quality Content
- 60% Fewer Hallucinations
Browse by: Latest US Patents, China's latest patents, Technical Efficacy Thesaurus, Application Domain, Technology Topic, Popular Technical Reports.
© 2025 PatSnap. All rights reserved.Legal|Privacy policy|Modern Slavery Act Transparency Statement|Sitemap|About US| Contact US: help@patsnap.com