Cutter wear monitoring method based on physical information fusion
A technology of tool wear and physical information, applied in manufacturing tools, measuring/indicating equipment, metal processing equipment, etc., to achieve the effect of reducing economic losses, low prediction errors, and reducing model complexity
- Summary
- Abstract
- Description
- Claims
- Application Information
AI Technical Summary
Problems solved by technology
Method used
Image
Examples
Embodiment Construction
[0036] In this embodiment, a tool wear monitoring method based on physical information fusion combines a physical model and a data-driven model to realize real-time high-precision tool wear monitoring, including: CNC machine tools, force sensors, industrial computers, and physical information algorithms:
[0037] In this embodiment, the CNC machine tool adopts the high-speed milling machining center Mikron HSM600U, which includes a bus interface and a sensor bracket, the force sensor is installed on the sensor bracket, and the milling cutters used are all three-blade milling cutters. The workpiece adopts AISI4340 square die. The workpiece was rough-milled before the experiment to ensure the flatness of the workpiece. The workpiece surface is cut in a zigzag shape by the tool from the upper edge to the lower edge. After each transverse cut, the wear of both edges was measured by a LEICAMZ12 microscope. During the processing of the workpiece, the cutting force signal is obtain...
PUM
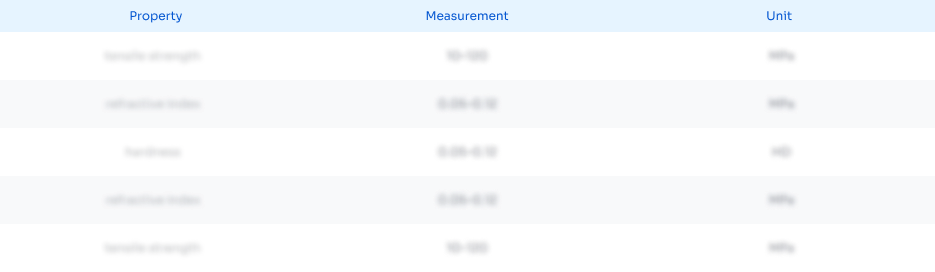
Abstract
Description
Claims
Application Information

- R&D
- Intellectual Property
- Life Sciences
- Materials
- Tech Scout
- Unparalleled Data Quality
- Higher Quality Content
- 60% Fewer Hallucinations
Browse by: Latest US Patents, China's latest patents, Technical Efficacy Thesaurus, Application Domain, Technology Topic, Popular Technical Reports.
© 2025 PatSnap. All rights reserved.Legal|Privacy policy|Modern Slavery Act Transparency Statement|Sitemap|About US| Contact US: help@patsnap.com