Industrial robot automatic tool workpiece calibration method
A technology of industrial robots and automatic tools, applied in the direction of manufacturing tools, manipulators, program-controlled manipulators, etc., can solve problems such as operational errors, low efficiency, and poor precision, and achieve the effect of improving contact accuracy
- Summary
- Abstract
- Description
- Claims
- Application Information
AI Technical Summary
Problems solved by technology
Method used
Image
Examples
Embodiment 1
[0045] The edge finder assembly can be replaced with higher cost ruby machine contacts:
[0046] Step 1: Connect all hardware parts according to the structure and connection relationship. Step 2: Operate the 4-industrial robot to make the 2-edge finder point in front of the 105-reference ball. At this time, the 2-edge finder is not in contact with the 105-reference ball. Step 3: Run the robot automatic calibration program, the robot will automatically find the 105-reference ball with a fixed posture, so that the 2-edge finder is in contact with the 105-reference ball. Step 4: 4- The robot automatically runs in a fixed posture and contacts the 105-reference ball three times, and records the three points P1, P2, and P3 respectively. Step 5: According to the three points P1, P2 and P3, find the center of the circle and calculate the coordinates of the center of the 109-robot running track. Step 6: Change 4- Robot Pose. Step 7: Repeat step 2, repeat step 3, repeat step 4, rep...
Embodiment 2
[0048] The reference ball is a calibration reference standard for machine tool processing, which can be processed by yourself or used by purchasing standard parts from suppliers:
[0049] Step 1: Connect all hardware parts according to the structure and connection relationship. Step 2: Operate the 4-industrial robot to make the 2-edge finder point in front of the 105-reference ball. At this time, the 2-edge finder is not in contact with the 105-reference ball. Step 3: Run the robot automatic calibration program, the robot will automatically find the 105-reference ball with a fixed posture, so that the 2-edge finder is in contact with the 105-reference ball. Step 4: 4- The robot automatically runs in a fixed posture and contacts the 105-reference ball three times, and records the three points P1, P2, and P3 respectively. Step 5: According to the three points P1, P2 and P3, find the center of the circle and calculate the coordinates of the center of the 109-robot running track....
PUM
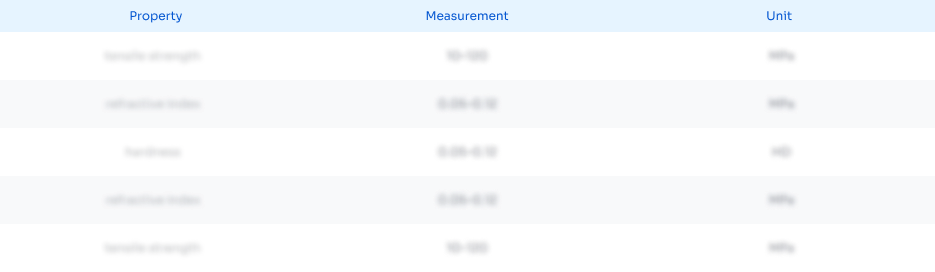
Abstract
Description
Claims
Application Information

- R&D
- Intellectual Property
- Life Sciences
- Materials
- Tech Scout
- Unparalleled Data Quality
- Higher Quality Content
- 60% Fewer Hallucinations
Browse by: Latest US Patents, China's latest patents, Technical Efficacy Thesaurus, Application Domain, Technology Topic, Popular Technical Reports.
© 2025 PatSnap. All rights reserved.Legal|Privacy policy|Modern Slavery Act Transparency Statement|Sitemap|About US| Contact US: help@patsnap.com