Thin-wall component variable-speed liquid filling-ultrasonic-laser composite forming method and system
A thin-walled component, composite forming technology, applied in the direction of forming tools, manufacturing tools, process efficiency improvement, etc., to achieve the effect of broadening the complexity, improving the forming performance, and improving the forming quality
- Summary
- Abstract
- Description
- Claims
- Application Information
AI Technical Summary
Problems solved by technology
Method used
Image
Examples
Embodiment Construction
[0033] Below in conjunction with accompanying drawing, the present invention will be described in further detail:
[0034] The variable-speed liquid-filling-ultrasonic-laser composite forming system for ultra-deep cavity complex thin-walled components provided by the present invention, see figure 1 , comprising a die 1, a punch 7, a blankholder 3, an ultrasonic vibration device, and a laser generator, the bottom of the die 1 is provided with a die liquid injection port 18, the upper part of the die 1 has a flange surface, and the die There is a die liquid chamber inside;
[0035] Described punch 7 is fixed on the die frame 9, and a plurality of ultrasonic vibrating devices are installed on the described die frame 9, and the bottom of each ultrasonic vibrating device is fixed on the crossbeam of punch 7, on the crossbeam lower surface of punch 7 A plurality of laser generators are installed, including the first laser generator 8 and the second laser generator 10. The lower par...
PUM
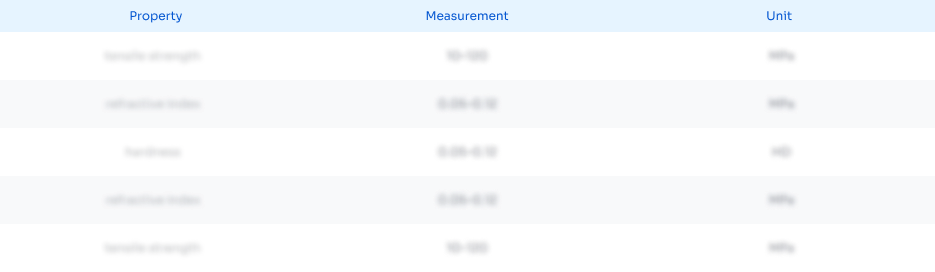
Abstract
Description
Claims
Application Information

- R&D
- Intellectual Property
- Life Sciences
- Materials
- Tech Scout
- Unparalleled Data Quality
- Higher Quality Content
- 60% Fewer Hallucinations
Browse by: Latest US Patents, China's latest patents, Technical Efficacy Thesaurus, Application Domain, Technology Topic, Popular Technical Reports.
© 2025 PatSnap. All rights reserved.Legal|Privacy policy|Modern Slavery Act Transparency Statement|Sitemap|About US| Contact US: help@patsnap.com