Method for producing bio-organic fertilizer by resource utilization of sugar refinery filter mud
A bio-organic fertilizer and sugar filter mud technology, which is applied in the preparation of organic fertilizers, the treatment of bio-organic parts, organic fertilizers, etc., can solve the problems of air pollution, production environment pollution, groundwater pollution, etc., and reduce the concentration of odorous substances , reduce the concentration of odor, overcome the effect of large floor area
- Summary
- Abstract
- Description
- Claims
- Application Information
AI Technical Summary
Problems solved by technology
Method used
Examples
Embodiment
[0036] S1: Dilute the sugar factory filter mud with a water content of 65%-75% to a water content of 80%-95%, and heat it at a constant temperature, the temperature is controlled at 150-190°C, and the heated filter mud enters the sedimentation Centrifuge, after the filter mud is separated by a sedimentation centrifuge, the separated sugar water enters the sugar water tank, which can further recover the 40%-60% sugar remaining in the wet filter mud; the water content of the filter mud separated by a sedimentation centrifuge is 48 %-52%, the filter mud separated by the settling centrifuge is transported to the stockpiling area by the conveyor belt;
[0037] S2: Evenly mix the filter mud settled by the decanting centrifuge with anaerobic fermentation bacteria to obtain mixed raw materials, wherein 3 kg of anaerobic bacteria are mixed with each ton of pre-fermentation product, and the mixed raw materials are piled into a pile with a ground diameter of 2m and a height of 1.5m, spra...
PUM
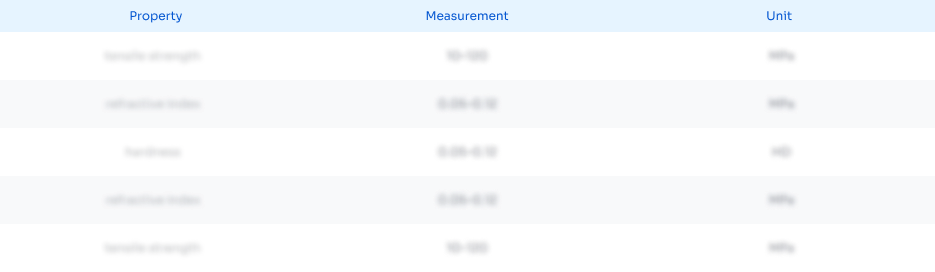
Abstract
Description
Claims
Application Information

- R&D Engineer
- R&D Manager
- IP Professional
- Industry Leading Data Capabilities
- Powerful AI technology
- Patent DNA Extraction
Browse by: Latest US Patents, China's latest patents, Technical Efficacy Thesaurus, Application Domain, Technology Topic, Popular Technical Reports.
© 2024 PatSnap. All rights reserved.Legal|Privacy policy|Modern Slavery Act Transparency Statement|Sitemap|About US| Contact US: help@patsnap.com