Adjustable cast-in-place support platform for pouring steel-concrete composite beam cantilever top plate
A technology of steel-concrete composite beams and support platforms, which is applied to buildings, bridges, bridge materials, etc., can solve the problems of high construction safety risks, unsecured construction personnel safety, and high safety risks, so as to improve spraying efficiency and spraying effect. , convenient for multi-directional spraying, and the effect of improving safety
- Summary
- Abstract
- Description
- Claims
- Application Information
AI Technical Summary
Problems solved by technology
Method used
Image
Examples
Embodiment 1
[0066] Such as Figure 1-10 As shown, a steel-concrete composite beam cantilever roof pouring adjustable cast-in-place support platform according to an embodiment of the present invention includes a support mechanism 1, a drive mechanism 2 installed on the support mechanism 1, and a drive mechanism 2 installed on the drive mechanism 2. The hanging mechanism 3 on the top and the spray mechanism 4 installed on the hanging mechanism 3;
[0067] Wherein, the supporting mechanism 1 includes a Bailey cantilever beam 101, both sides of the bottom of the Bailey cantilever beam 101 are fixedly connected with a support section steel 102, and the bottom of the support section steel 102 is fixedly connected with a support base 103;
[0068] Wherein, the driving mechanism 2 includes a first driving frame 201 and a second driving frame 202 symmetrically connected to both sides of the bottom of the Bailey beam 101, and the side of the second driving frame 202 is fixedly connected with a serv...
Embodiment 2
[0082] Such as Figure 1-10 As shown, the difference between this embodiment and Embodiment 1 is that the tops of the inner walls of the first driving frame 201 and the second driving frame 202 are fixedly connected with mounting blocks 2091, and the two mounting blocks 2091 are fixed between Two guiding slides 2092 are connected, and symmetrically arranged guide sliding sleeves 2093 are slidably connected to the guiding slides 2092, and the bottom of the guide sliding sleeves 2093 is fixedly connected with the top of the installation frame 209, and the top plate The four corners of the top of 211 are fixedly connected with reinforcing ribs 2111 , and the other end of the reinforcing ribs 2111 is fixedly connected with the corners of the bottom of the installation frame 209 .
[0083] By adopting the above technical solution, the installation frame 209 can be limited, thereby increasing the sliding stability of the installation frame 209 and increasing the installation stabili...
Embodiment 3
[0085] Such as Figure 1-10 As shown, the difference between this embodiment and Embodiment 2 is that the bottom mounting ear 3022 is fixedly mounted on the top of the bottom plate 3012 through mounting screws, and the top mounting ear 3025 is fixedly mounted on the construction surface through mounting screws. The bottom of platform 3014.
[0086]By adopting the above technical solution, it is convenient to disassemble and install the jack 3023, thereby facilitating the maintenance of the jack 3023.
PUM
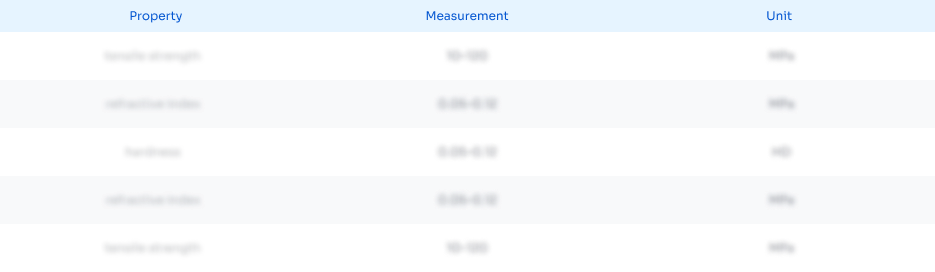
Abstract
Description
Claims
Application Information

- Generate Ideas
- Intellectual Property
- Life Sciences
- Materials
- Tech Scout
- Unparalleled Data Quality
- Higher Quality Content
- 60% Fewer Hallucinations
Browse by: Latest US Patents, China's latest patents, Technical Efficacy Thesaurus, Application Domain, Technology Topic, Popular Technical Reports.
© 2025 PatSnap. All rights reserved.Legal|Privacy policy|Modern Slavery Act Transparency Statement|Sitemap|About US| Contact US: help@patsnap.com