Evaluation process for gas-phase stirred bed catalyst
A catalyst and stirred bed technology, which is applied in the field of polyolefin catalyst polymerization evaluation process, can solve the problems of uneven catalyst dispersion, lack of catalyst, large particles, etc., and achieve good polymerization performance, less agglomeration, and cost reduction.
- Summary
- Abstract
- Description
- Claims
- Application Information
AI Technical Summary
Problems solved by technology
Method used
Image
Examples
Embodiment 1
[0050] Described gas-phase stirred bed catalyst evaluation process, specific operation steps are as follows:
[0051] 1. Pretreatment of the polymerization kettle, drying the polymerization kettle in the oven for 2 hours, then putting on the kettle, and vacuuming the polymerization kettle, keeping the vacuum to -0.1MPa for 10 minutes, then replenishing nitrogen to 0.1MPa, and then Vent the nitrogen and repeat the operation at least three times. After the operation, the pressure in the kettle was maintained at 0.1MPa.
[0052] 2. Preheat the polymerization kettle, start the polymerization kettle to stir, open the temperature control system to raise the temperature of the polymerization kettle, and control the preheating temperature to 50°C.
[0053] 3. Add catalyst, through figure 1 The feeder shown adds the catalyst to the polymerization tank, and the steps are as follows:
[0054] 3.1 Empty the polymerization kettle, then evacuate to -0.1MPa, and close the vacuum valve.
...
Embodiment 2
[0068] Test process is as embodiment 1, wherein:
[0069] Step 2: The polymerization kettle is pre-heated, and the temperature is 65°C.
[0070] Step 3.4 The stirring speed is 300 rpm.
[0071] Step 3.6 The flow rate of nitrogen gas is 150mL / min.
[0072] The analysis results are shown in Table 1.
Embodiment 3
[0074] Test process is as embodiment 1, wherein:
[0075] Step 2: The polymerization kettle is pre-heated, and the temperature is 75°C.
[0076] Step 3.4 The stirring speed is 400 rpm.
[0077] Step 3.6 nitrogen 200mL / min.
[0078] The analysis results are shown in Table 1.
PUM
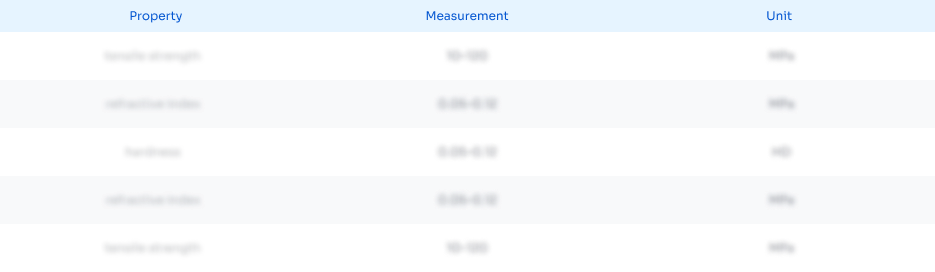
Abstract
Description
Claims
Application Information

- Generate Ideas
- Intellectual Property
- Life Sciences
- Materials
- Tech Scout
- Unparalleled Data Quality
- Higher Quality Content
- 60% Fewer Hallucinations
Browse by: Latest US Patents, China's latest patents, Technical Efficacy Thesaurus, Application Domain, Technology Topic, Popular Technical Reports.
© 2025 PatSnap. All rights reserved.Legal|Privacy policy|Modern Slavery Act Transparency Statement|Sitemap|About US| Contact US: help@patsnap.com