Method for monitoring safe operation of catalytic oil-free compression system
A technology of compression system and safe operation, applied in chemical instruments and methods, separation methods, pump testing, etc., can solve the problems of lag in detection data, inability to effectively ensure user gas quality, and inability to provide early feedback
- Summary
- Abstract
- Description
- Claims
- Application Information
AI Technical Summary
Problems solved by technology
Method used
Image
Examples
Embodiment 1
[0029] The method for monitoring the safe operation of the catalytic oil-free compression system of the present invention uses a catalytic oil-free compression system such as figure 1 As shown in , including compressor, oil-gas separator (not shown), gas-liquid separator 2, catalytic converter 6, heat exchanger, first oil content detection device 13, second oil content detection device 11, electronic cooling 9, filter adsorption tank 10, radiator 12, gas-liquid separation exhaust pipe 3, display screen (not shown) and alarm (not shown), the compressor adopts oil-injected screw compressor 1, and radiator 12 is installed Above the oil-injected screw compressor 1 , the oil-injected screw compressor 1 compresses air and is lubricated with lubricating oil during operation, and the radiator 12 radiates heat and cools down the oil-injected screw compressor 1 in time. The heat exchanger adopts a partition-type heat exchanger 4, and the partition-type heat exchanger 4 is provided with ...
Embodiment 2
[0040] The difference between the method for monitoring the safe operation of the catalytic oil-free compression system in this embodiment and that in Embodiment 1 is that in the catalytic oil-free compression system adopted in this embodiment, the catalytic intake pipe 5 is provided with a catalytic converter intake pipe and a pair of The air exhaust pipe, the catalytic converter intake pipe is connected and communicated with the air inlet of the catalytic converter, the catalytic converter intake pipe is used to introduce compressed gas into the catalytic converter, and the empty exhaust pipe is not connected with the air intake of the catalytic converter. The air discharge pipe is used to discharge the compressed gas to the air. Valves are arranged in both the intake pipe of the catalytic converter and the air discharge pipe. Open the valve of the catalytic air intake pipe to introduce the compressed gas into the catalytic converter, and close the valve to the empty exhaust ...
Embodiment 3
[0042] The difference between the method for monitoring the safe operation of the catalytic oil-free compression system in this embodiment and that in Embodiment 1 is that in the catalytic oil-free compression system used in this embodiment, the heat exchange exhaust pipe 8 is provided with an air supply pipe and a pair of The air exhaust pipe and the air supply pipe are used to connect and supply gas to the gas-consuming equipment, and the air-to-air exhaust pipe is used to discharge compressed gas to the air. Valves are arranged on the air-supply pipe and the air-to-air exhaust pipe. When the catalytic oil-free compression system is running normally and the oil content of the compressed gas does not exceed the standard, the valve of the gas supply pipe can be opened and the valve of the air exhaust pipe can be closed. The catalytic oil-free compression system of the present invention passes through the gas supply pipe Continuously supply gas to the user's gas equipment to ens...
PUM
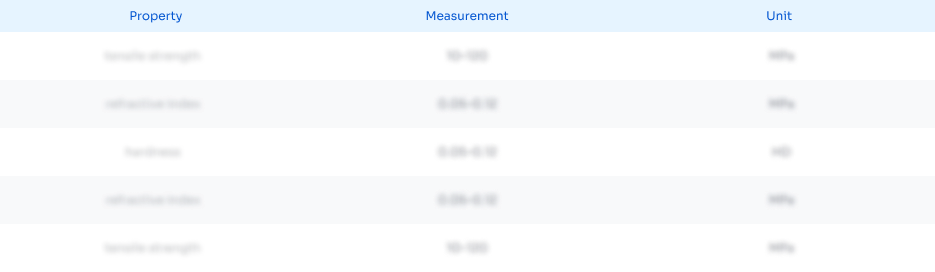
Abstract
Description
Claims
Application Information

- Generate Ideas
- Intellectual Property
- Life Sciences
- Materials
- Tech Scout
- Unparalleled Data Quality
- Higher Quality Content
- 60% Fewer Hallucinations
Browse by: Latest US Patents, China's latest patents, Technical Efficacy Thesaurus, Application Domain, Technology Topic, Popular Technical Reports.
© 2025 PatSnap. All rights reserved.Legal|Privacy policy|Modern Slavery Act Transparency Statement|Sitemap|About US| Contact US: help@patsnap.com