Quick filling vertical pipeline simulation method considering intercepted air energy dissipation
A technology of trapping air and dissipating energy, applied in CAD numerical modeling, instrumentation, design optimization/simulation, etc., can solve the problem of not considering the heat transfer energy loss of trapped cavitation, unable to explain the phenomenon of white fog and heat pipe wall, underestimating Problems such as pressure decay rate to achieve the effect of solving transient simulation problems
- Summary
- Abstract
- Description
- Claims
- Application Information
AI Technical Summary
Problems solved by technology
Method used
Image
Examples
Embodiment 1
[0120] The experimental data measured in a vertical pipeline with a clear air-water interface in the pipeline hydraulic transient experimental device system designed and built by Zhou in 2018 is selected to verify the effectiveness of the method for simulating the pressure oscillation in a fast-filling pipeline with an interception airbag.
[0121] In this embodiment, the upstream pressure vessel (relative pressure Pr) is connected to an 8.862m long, 4cm inner diameter pipe at the end, which is composed of an 8.382m long horizontal pipe and a 0.48m long terminal vertical pipe. At first, the control valve is completely closed, and the trapped air pocket La0 is at atmospheric pressure, and the valve opens instantly.
[0122] Comparing the simulation results of the method of the present invention with the above simulation results, we can get the results as follows Figure 4 The pressure curve shown by Figure 4 It can be seen that the heat transfer model considering steady friction, un...
Embodiment 2
[0124] The simulation results of the model with traditional empirical multi-party relationship are selected to verify the effectiveness of the new heat transfer model to simulate energy dissipation.
[0125] In this example, the constant polytropic index m of adiabatic process (without heat transfer) is m=1.4, and TVB turbulence model is used to simulate the unsteady friction.
[0126] Comparing the simulation results of the method of the present invention with the above simulation results, we can get the results as follows Figure 5 The pressure curve shown by Figure 5 It can be seen that the heat transfer model provided by the invention can accurately simulate the energy dissipation of the system; However, the empirical multi-party relationship method with adiabatic hypothesis can only accurately reproduce the pressure and temperature during the first two oscillations of the system test, and with the rapid filling event advancing, the oscillation peak value and time will be great...
PUM
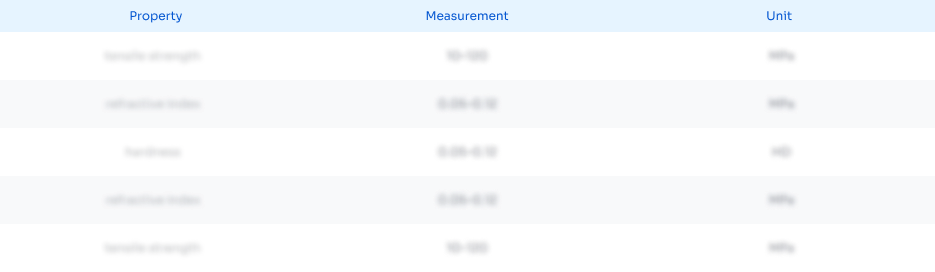
Abstract
Description
Claims
Application Information

- R&D
- Intellectual Property
- Life Sciences
- Materials
- Tech Scout
- Unparalleled Data Quality
- Higher Quality Content
- 60% Fewer Hallucinations
Browse by: Latest US Patents, China's latest patents, Technical Efficacy Thesaurus, Application Domain, Technology Topic, Popular Technical Reports.
© 2025 PatSnap. All rights reserved.Legal|Privacy policy|Modern Slavery Act Transparency Statement|Sitemap|About US| Contact US: help@patsnap.com