Effect powder for sinking ink as well as preparation method and application of effect powder
An effect powder and ink technology, applied in the field of ceramic powder, can solve the problems of insufficient texture, coherence, yellow-green residue, etc., and achieve the effect of improving crushing and grinding efficiency, no color residue, and fine subsidence texture.
- Summary
- Abstract
- Description
- Claims
- Application Information
AI Technical Summary
Problems solved by technology
Method used
Image
Examples
Embodiment 1
[0031] The effect powder for sinking ink of the present embodiment includes the following raw materials in parts by weight:
[0032] Nepheline: 13 parts
[0033] Quartz: 30 parts
[0034] Lead oxide: 17 parts
[0035] Vanadium pentoxide: 40 parts.
[0036] A method for preparing an effect powder for sinking ink in this embodiment comprises the following steps:
[0037] a. Weighing: Weigh the raw materials according to the above formula, put them into the dry powder mixer, mix the raw materials fully and evenly to form a mixture, put it into a sagger, and cover it with a lid.
[0038] b. Calcination: Put the sagger with the mixed material on the kiln car to enter the tunnel kiln for calcination. The calcination temperature is 700° C., and the calcination time is 10 hours. After heat preservation, it is naturally cooled to room temperature to obtain the calcined material.
[0039] c. Crushing and grinding: use a crusher to crush the calcined material, and then process it thr...
Embodiment 2
[0041] The effect powder for sinking ink of the present embodiment includes the following raw materials in parts by weight:
[0042] Nepheline: 10 parts
[0043] Quartz: 37 parts
[0044] Lead oxide: 23 parts
[0045] Vanadium pentoxide: 30 parts.
[0046] A method for preparing an effect powder for sinking ink in this embodiment comprises the following steps:
[0047] a. Weighing: Weigh the raw materials according to the above formula, put them into the dry powder mixer, mix the raw materials fully and evenly to form a mixture, put it into a sagger, and cover it with a lid.
[0048] b. Calcination: Put the sagger with the mixed material on the kiln car to enter the tunnel kiln for calcination. The calcination temperature is 1000° C., and the calcination time is 8 hours. After heat preservation, it is naturally cooled to room temperature to obtain the calcined material.
[0049] c. Crushing and grinding: use a crusher to crush the calcined material, and then process it throu...
Embodiment 3
[0051] The effect powder for sinking ink of the present embodiment includes the following raw materials in parts by weight:
[0052] Quartz: 37 parts
[0053] Lead oxide: 23 parts
[0054] Vanadium pentoxide: 40 parts.
[0055] A method for preparing an effect powder for sinking ink in this embodiment comprises the following steps:
[0056] a. Weighing: Weigh the raw materials according to the above formula, put them into the dry powder mixer, mix the raw materials fully and evenly to form a mixture, put it into a sagger, and cover it with a lid.
[0057] b. Calcination: Put the sagger with the mixed material on the kiln car to enter the tunnel kiln for calcination. The calcination temperature is 750° C., and the calcination time is 6 hours. After heat preservation, it is naturally cooled to room temperature to obtain the calcined material.
[0058] c. Crushing and grinding: use a crusher to crush the calcined material, and then process it through a jet mill until the D of ...
PUM
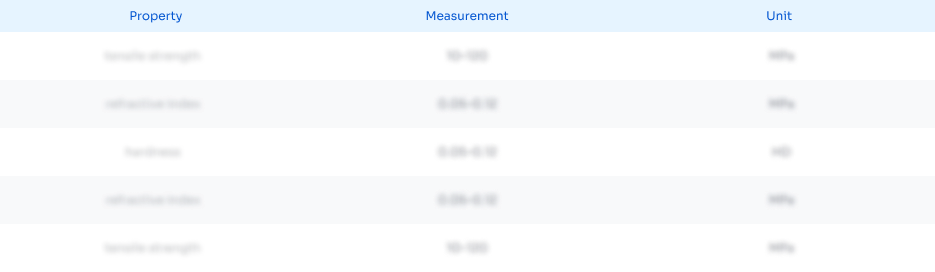
Abstract
Description
Claims
Application Information

- Generate Ideas
- Intellectual Property
- Life Sciences
- Materials
- Tech Scout
- Unparalleled Data Quality
- Higher Quality Content
- 60% Fewer Hallucinations
Browse by: Latest US Patents, China's latest patents, Technical Efficacy Thesaurus, Application Domain, Technology Topic, Popular Technical Reports.
© 2025 PatSnap. All rights reserved.Legal|Privacy policy|Modern Slavery Act Transparency Statement|Sitemap|About US| Contact US: help@patsnap.com