Nylon 12 composite material for MJR3D printing and preparation method thereof
A composite material and nylon technology, applied in the field of additive manufacturing, can solve the shortage of polymer 3D printing materials and other problems
- Summary
- Abstract
- Description
- Claims
- Application Information
AI Technical Summary
Problems solved by technology
Method used
Image
Examples
Embodiment 1
[0032] A preparation of a new type of nylon 12 composite material for MJR 3D printing, the specific process is as follows:
[0033] (1) PA12 powder for surface nickel activation
[0034] Add 20 ml of KH550, 10 ml of deionized water and 30 ml of ethanol into a beaker, and mix at 40°C for 1 hour at a stirring speed of 400 rpm to obtain a KH550 solution. Add 5 g of PA12 powder and 100 ml of ethanol to the KH550 solution, stir slowly in a water bath at 60 °C for 0.5 h, and then rinse twice with deionized water and ethanol to obtain KH550 surface-modified nylon 12 powder.
[0035] Then add 3g of nickel acetate particles into 100ml of deionized water to form a 30g / ml nickel acetate solution, then add the above-mentioned surface-modified nylon 12 powder into the 30g / ml nickel acetate solution, transfer to a 60°C water bath and stir at 400rpm Speed mixing, the reaction time is 1h, and then the obtained product is washed with deionized water and ethanol, and then vacuum-dried to obt...
Embodiment 2
[0041] A preparation of a new type of nylon 12 composite material for MJR 3D printing, the specific process is as follows:
[0042] (1) PA12 powder for surface nickel activation
[0043] Add 20 ml of KH550, 10 ml of deionized water and 30 ml of ethanol into a beaker, and mix at 40°C for 1 hour at a stirring speed of 400 rpm to obtain a KH550 solution. Add 5 g of PA12 powder and 100 ml of ethanol to the KH550 solution, stir slowly in a water bath at 60 °C for 0.5 h, and then rinse twice with deionized water and ethanol to obtain KH550 surface-modified nylon 12 powder.
[0044] Then add 3g of nickel acetate particles into 100ml of deionized water to form a 30g / ml nickel acetate solution, then add the above-mentioned surface-modified nylon 12 powder into the 30g / ml nickel acetate solution, transfer to a 60°C water bath and stir at 40rpm Speed mixing, the reaction time is 1h, and then the obtained product is washed with deionized water and ethanol, and then vacuum-dried to obta...
Embodiment 3
[0050] A preparation of a new type of nylon 12 composite material for MJR 3D printing, the specific process is as follows:
[0051] (1) PA12 powder for surface nickel activation
[0052] Add 20 ml of KH550, 10 ml of deionized water and 30 ml of ethanol into a beaker, and mix at 40°C for 1 hour at a stirring speed of 400 rpm to obtain a KH550 solution. Add 5 g of PA12 powder and 100 ml of ethanol to the KH550 solution, stir slowly in a water bath at 60 °C for 0.5 h, and then rinse twice with deionized water and ethanol to obtain KH550 surface-modified nylon 12 powder.
[0053] Then add 3g of nickel acetate particles into 100ml of deionized water to form a 30g / ml nickel acetate solution, then add the above-mentioned surface-modified nylon 12 powder into the 30g / ml nickel acetate solution, transfer to a 60°C water bath and stir at 400rpm Speed mixing, the reaction time is 1h, and then the obtained product is washed with deionized water and ethanol, and then vacuum-dried to obt...
PUM
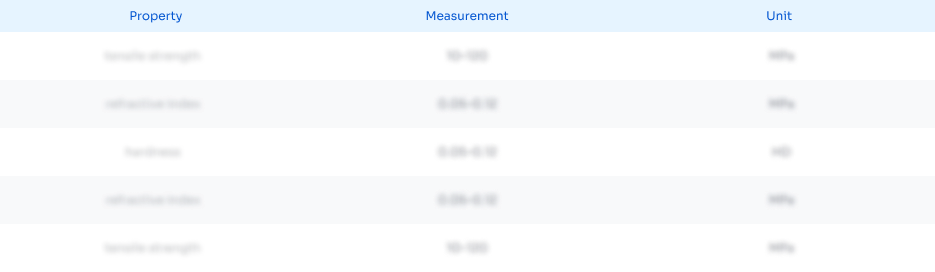
Abstract
Description
Claims
Application Information

- Generate Ideas
- Intellectual Property
- Life Sciences
- Materials
- Tech Scout
- Unparalleled Data Quality
- Higher Quality Content
- 60% Fewer Hallucinations
Browse by: Latest US Patents, China's latest patents, Technical Efficacy Thesaurus, Application Domain, Technology Topic, Popular Technical Reports.
© 2025 PatSnap. All rights reserved.Legal|Privacy policy|Modern Slavery Act Transparency Statement|Sitemap|About US| Contact US: help@patsnap.com