Synthesis method for preparing anilino piperidine medicine by using continuous flow microchannel reactor
A channel reactor and anilinopiperidine technology, which is applied in chemical instruments and methods, chemical/physical processes, chemical/physical/physical chemical processes, etc., can solve the problem of labor hours and energy consumption, increase product production costs, Problems such as low conversion rate and selectivity, to achieve the effect of reducing material loss, improving mass transfer, conversion rate and selectivity
- Summary
- Abstract
- Description
- Claims
- Application Information
AI Technical Summary
Problems solved by technology
Method used
Image
Examples
Embodiment 1
[0078] 20.0 g of Compound I and 9.0 g of triethylamine, added to 200 ml of methyl isobutyl ketone, stir mixed, pumped from the feed port A of the module 1, and the flow rate was 30 mL / min; weigh 19.0 g of a compound II was added to 110 ml of methyl isobutyl ketone, stirred and mixed, pumped from the feed port B of the module 1 into the reactor, and the flow rate was 15 mL / min. The temperature of the modules 1-6 is controlled to 107 ° C, and the temperature of the module 7 is controlled to 50 ° C, the sample detection reaction conversion is 99.30%, HPLC map, see figure 1 . In the module 8, the purified water is pumped, the flow rate is 30 ml / min, and the material flows out of the module 8 is collected in the tank.
[0079] The material in the tank was discharged, and the liquid was allowed to collect organic phases; the organic phase was washed with saturated aqueous solution of sodium chloride, and then dried over anhydrous sulfate for 3 hours. 10 ml of concentrated hydrochl...
Embodiment 2
[0082] 20.0 g of a compound I and 17.0 g of potassium carbonate were weighed, and the mixture was added to 300 ml of toluene, stir mixed, pumped from the feed port A of the module 1, and the flow rate was 20 ml / min; weigh 23.0 g of Compound II to add to In 200 ml of toluene, stir mix, pumped from the feed port B of the module 1 to the reactor, and the flow rate was 13 mL / min. The temperature of the modules 1-6 is controlled to 103 ° C, and the temperature of the module 7 is controlled to 50 ° C, the sample detection reaction conversion is 97.23%, HPLC map, see image 3 . In the module 8, the purified water is pumped, the flow rate is 50 ml / min, and the material flows out of the module 8 is collected in the tank.
[0083] The material in the storage tank was released, and the liquid was allowed to collect organic phases; the organic phase was washed with saturated aqueous sodium chloride solution, and then dried in anhydrous carbon chloride for 4 hours, filtered, filtrate was ...
Embodiment 3
[0086] 20.0 g of Compound I and 10.0 g of triethylamine were weighed, and the mixture was mixed into 150 mL of ethyl acetate, stirred, pumped from the feed port A of the module 1, and the flow rate was 20 ml / min; weigh 22.0 g of Compound III added to 1000 ml of ethyl acetate, stirred and mixed, pumped from the feed port B of the module 1 into the reactor, and the flow rate was 15 mL / min. The temperature of the modules 1-6 is controlled to 68 ° C, the temperature of the module 7 is controlled to 30 ° C, the sample detection reaction conversion is 97.13%, HPLC map, see Figure 5 . In the module 8, the purified water is pumped, the flow rate is 30 ml / min, and the material flows out of the module 8 is collected in the tank.
[0087] The material in the tank was released, replaced, collected by the organic phase; the organic phase was washed with saturated aqueous solution of sodium chloride, and then dried over anhydrous sodium sulfate for 4 hours, filtered, filtrate was concentr...
PUM
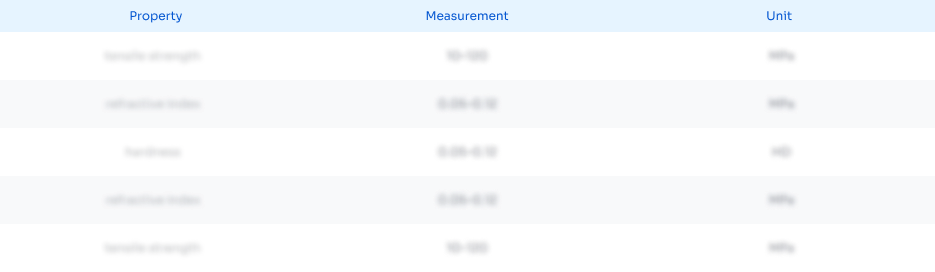
Abstract
Description
Claims
Application Information

- R&D
- Intellectual Property
- Life Sciences
- Materials
- Tech Scout
- Unparalleled Data Quality
- Higher Quality Content
- 60% Fewer Hallucinations
Browse by: Latest US Patents, China's latest patents, Technical Efficacy Thesaurus, Application Domain, Technology Topic, Popular Technical Reports.
© 2025 PatSnap. All rights reserved.Legal|Privacy policy|Modern Slavery Act Transparency Statement|Sitemap|About US| Contact US: help@patsnap.com