Recycled fine aggregate high-strength self-compacting concrete and preparation method thereof
A technology of self-compacting concrete and recycled fine aggregate, applied in the field of concrete, can solve the problems that concrete cannot strengthen the preparation operation, reduce the molding effect, and unfavorable use, and achieve excellent frost resistance, increase molding effect, and increase work performance.
- Summary
- Abstract
- Description
- Claims
- Application Information
AI Technical Summary
Problems solved by technology
Method used
Examples
Embodiment 1
[0023] A kind of recycled fine aggregate high-strength self-compacting concrete, including artificial sand fine aggregate, perlite aggregate, cement, cement, ultrafine mineral powder, water and reinforcing mixed materials, the proportion of artificial sand fine aggregate is 18-30 %, the share of perlite aggregate is 15-22%, the share of cement is 10-15%, the share of cement is 12-19%, the share of ultrafine mineral powder is 10-16%, and the share of water is 10% -20%, the share of reinforcing mixed materials is 10-20%.
[0024] Further, the share of artificial sand fine aggregate is 23%, the share of perlite aggregate is 15%, the share of cement is 11%, the share of cement is 13%, the share of ultrafine mineral powder is 14%, water The share of 13% and 11% of reinforced mixed materials.
[0025] A method for preparing recycled fine aggregate high-strength self-compacting concrete, comprising the following steps:
[0026] S1: Prepare the materials needed for the preparation o...
Embodiment 2
[0035] On the basis of Example 1, a recycled fine aggregate high-strength self-compacting concrete, including artificial sand fine aggregate, perlite aggregate, cement, cement, ultrafine mineral powder, water and reinforcing mixed materials, artificial sand fine aggregate The share of aggregate is 18-30%, the share of perlite aggregate is 15-22%, the share of cement is 10-15%, the share of cement is 12-19%, and the share of ultrafine mineral powder is 10- 16%, the share of water is 10-20%, the share of reinforcing mixed material is 10-20%.
[0036] Further, the share of artificial sand fine aggregate is 20%, the share of perlite aggregate is 16%, the share of cement is 12%, the share of cement is 14%, the share of ultrafine mineral powder is 13%, water The share of 11% and 14% of reinforced hybrid materials.
[0037] A method for preparing recycled fine aggregate high-strength self-compacting concrete, comprising the following steps:
[0038] S1: Prepare the materials needed...
Embodiment 3
[0047] On the basis of Embodiment 1 and Embodiment 2, a recycled fine aggregate high-strength self-compacting concrete, including artificial sand fine aggregate, perlite aggregate, cement, cement, ultrafine mineral powder, water and reinforcing mixed materials , the share of artificial sand fine aggregate is 18-30%, the share of perlite aggregate is 15-22%, the share of cement is 10-15%, the share of cement is 12-19%, and the share of ultrafine mineral powder The share is 10-16%, the share of water is 10-20%, the share of reinforcing mixed material is 10-20%.
[0048] Further, the share of artificial sand fine aggregate is 23%, the share of perlite aggregate is 15%, the share of cement is 11%, the share of cement is 13%, the share of ultrafine mineral powder is 14%, water The share of 13% and 11% of reinforced mixed materials.
[0049] A method for preparing recycled fine aggregate high-strength self-compacting concrete, comprising the following steps:
[0050] S1: Prepare t...
PUM
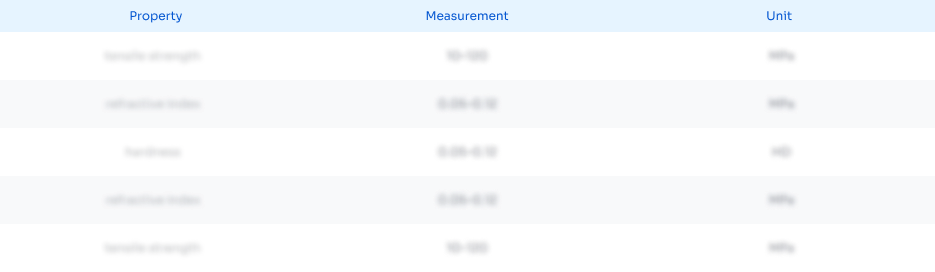
Abstract
Description
Claims
Application Information

- R&D Engineer
- R&D Manager
- IP Professional
- Industry Leading Data Capabilities
- Powerful AI technology
- Patent DNA Extraction
Browse by: Latest US Patents, China's latest patents, Technical Efficacy Thesaurus, Application Domain, Technology Topic, Popular Technical Reports.
© 2024 PatSnap. All rights reserved.Legal|Privacy policy|Modern Slavery Act Transparency Statement|Sitemap|About US| Contact US: help@patsnap.com