Machining of sheet without removal material
A plate and flat plate technology, which is applied in the field of plate mechanical processing without removing materials and its devices, can solve the problems of high speed of advancement, difficulty in obtaining products without bending and rolling, etc.
- Summary
- Abstract
- Description
- Claims
- Application Information
AI Technical Summary
Problems solved by technology
Method used
Image
Examples
Embodiment Construction
[0022] The processing device shown in Figures 1 to 4 comprises a frame 11 which supports a clamping device 16 holding two flat plates 161 and 162 mounted opposite each other so as to form a nominal opening between said flat plates 161 and 162 1. The device comprises a means for forcing the movement of the sheet relative to the nominal opening, ie a platen 15 capable of gripping the sheet 2 and moving relative to said plates 161 and 162 . This pressing plate 15 pulls the sheet 2 . In a movement away from the plates 161 and 162 , the platen is not too far from the plane perpendicular to the plane of the nominal opening 1 and passing through said opening.
[0023] In other words, the sheet passes through the nominal openings constituting a die not for drawing the wire, but for processing the sheet. However, the present invention is quite different from the analogous case of drawing because of the shape of the opening formed, which forms a new dimension for the sheet.
[0024] ...
PUM
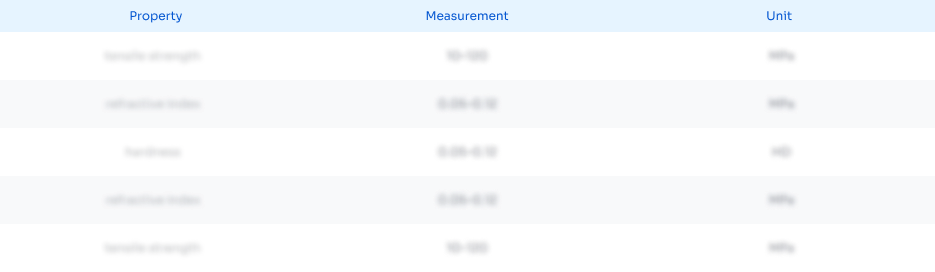
Abstract
Description
Claims
Application Information

- R&D Engineer
- R&D Manager
- IP Professional
- Industry Leading Data Capabilities
- Powerful AI technology
- Patent DNA Extraction
Browse by: Latest US Patents, China's latest patents, Technical Efficacy Thesaurus, Application Domain, Technology Topic, Popular Technical Reports.
© 2024 PatSnap. All rights reserved.Legal|Privacy policy|Modern Slavery Act Transparency Statement|Sitemap|About US| Contact US: help@patsnap.com